The field of injection molding has seen significant advancements in recent years, driven by emerging technologies that are transforming the way products are designed, manufactured, and optimized. From enhanced precision and efficiency to reduced production costs, these innovations are not only improving the quality of molded parts but also enabling manufacturers to meet the increasing demand for complex and customizable products. This article explores the key technological advances fueling innovation in injection molding, highlighting their impact on various industries and their potential to shape the future of manufacturing.
Enhanced Mold Technology
Investments in mold technology lead to substantial changes in the injection molding process. New techniques such as conformal cooling and multi-cavity molds minimize cycle times and improve product quality. Conformal cooling, for instance, uses advanced mold designs that allow for optimized coolant flow, resulting in balanced cooling rates.
This technique directly influences the precision of molded parts and reduces production costs. Moreover, innovations in the production of injection molding mold parts enhance durability and cost-efficiency. Advanced materials for mold construction, combined with innovative manufacturing processes, reduce wear and maintain consistent performance. As a result, manufacturers can expect an increase in mold lifespan, translating into sustained profitability over time.
Advanced Materials and Polymer Science
The evolution of materials used in injection molding significantly impacts product quality and performance. Innovations in polymer science led to the development of engineered thermoplastics and composites that offer enhanced strength, durability, and resistance to harsh environments. These advanced materials allow manufacturers to produce injection molding parts that meet stringent industry regulations while minimizing weight and maximizing performance.
Additionally, the emergence of bio-based materials has gained traction, driven by a push for sustainable manufacturing practices. These materials, derived from renewable resources, contribute to reduced environmental impact and align with the growing consumer demand for eco-friendly products. As research continues to advance in materials science, companies can expect an even broader selection of options to choose from, further enhancing their production capabilities and market competitiveness.
Automation and Robotics
The integration of automation and robotics into injection molding processes marks a significant technological advancement. Robotic systems are employed to streamline various stages of production, from material handling to part finishing. This automation minimizes human error and enhances precision in the manufacturing process, allowing for more intricate designs and higher output rates.
Moreover, automation enables manufacturers to achieve significant cost savings by reducing labor expenses and optimizing production workflows. With advanced robotics, companies can increase their operational efficiency, allowing them to focus on innovation and improving product quality. This shift towards an automated setup also supports the scalability of operations, allowing manufacturers to adapt quickly to changes in demand.
Smart Manufacturing Technologies
The rise of smart manufacturing technologies, including the Internet of Things (IoT) and Industry 4.0, is changing how injection molding processes are managed. These technologies facilitate real-time monitoring and data analysis throughout the production cycle, improving decision-making and operational efficiency. By connecting machines and systems, manufacturers gain insights into performance metrics, leading to proactive maintenance and reduced downtime.
As predictive analytics become integrated into production environments, manufacturers can forecast potential issues before they escalate. This predictive capability allows companies to adhere to stricter quality control measures, ensuring that each product meets predefined specifications. Additionally, the utilization of real-time data enhances supply chain management, allowing businesses to track inventory levels and streamline logistics.
Simulation and Design Software
Investments in simulation and design software are essential for advancing injection molding technology. These tools reduce the time and cost associated with physical prototyping by allowing engineers to visualize and test designs in a virtual environment. Engineers can simulate the injection molding process to identify potential defects, optimize cycle times, and improve overall design efficiency.
By utilizing simulated environments, manufacturers can make informed adjustments to the production process before implementing changes in reality. This capability streamlines the development of new products and reduces lead times, ultimately accelerating time-to-market. Enhanced design software ensures that companies can craft intricate and detailed designs, setting the stage for high-quality production.
Short-Run Manufacturing
Technological advancements have also enabled short-run manufacturing—the ability to produce small batches of parts at a competitive price. This shift caters to market trends where customization and flexibility are paramount. Today’s consumers often seek specialized products, compelling manufacturers to respond rapidly to these requests. Injection molding technology has evolved to support lower production runs without compromising quality or efficiency.
Short-run manufacturing is particularly advantageous for testing new products or entering niche markets. By employing technologies such as rapid prototyping and advanced molds, companies can produce specialized parts without significant upfront investment. This allows businesses to place focus on innovation and iteration while meeting customer demands effectively.
The injection molding industry is on a path of dynamic change thanks to technological advancements that embrace innovation and efficiency. From advanced materials to automation and smart manufacturing, each new development contributes to creating better products and fostering a competitive environment. As the industry continues to grow and evolve, companies that leverage these technologies will find themselves well-positioned to navigate future challenges, ensuring that they remain at the forefront of manufacturing excellence.
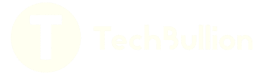