In the dynamic landscape of modern manufacturing, innovation is no longer optional – it’s a necessity. Deepak Bajaj’s insightful analysis into the evolution of AI-driven smart factories and predictive maintenance systems brings forward a captivating narrative of how artificial intelligence (AI) is reshaping industrial processes. Combining expertise with practical insights, this exploration delves into the transformative journey of these groundbreaking technologies.
Bridging Gaps with Smart Factories
Traditional manufacturing has often been constrained by inefficiencies, rigid workflows, and limited adaptability. Enter smart factories, a revolutionary leap powered by AI and IoT technologies, designed to overcome these limitations. These cutting-edge facilities utilize interconnected systems, advanced sensors, and real-time analytics to create adaptive, highly efficient production ecosystems.
A key innovation within smart factories is automated decision-making. AI algorithms process vast amounts of data to monitor equipment performance, predict maintenance needs, and optimize workflows. This reduces human error, minimizes downtime, and significantly boosts productivity.
Additionally, smart factories excel in resource management. By analyzing consumption patterns and predicting future demands, they ensure just-in-time resource allocation, reducing waste and fostering sustainability. This aligns with global efforts toward eco-friendly practices, addressing critical environmental concerns.
In essence, smart factories merge intelligence with efficiency, offering manufacturers the agility to innovate, adapt, and thrive in an ever-evolving industrial landscape.
The Power of Predictive Maintenance
Downtime in manufacturing can be a costly affair, often stemming from unexpected equipment failures. Enter predictive maintenance systems – a game-changer enabled by AI. These systems collect data from machinery in real time, using advanced algorithms to forecast potential issues before they occur.
This proactive approach saves time and money while ensuring worker safety. For instance, by identifying anomalies in equipment behavior, manufacturers can schedule maintenance during planned downtimes rather than scrambling to address sudden breakdowns. The result is a seamless operation that boosts both efficiency and reliability.
Predictive maintenance also fosters a culture of continuous improvement. By learning from historical data, these systems refine their predictions over time, making them more accurate and insightful. This iterative process ensures that manufacturing facilities remain agile in the face of evolving challenges.
AI as the Backbone of Transformation
Artificial intelligence (AI) is the backbone of smart factory innovations, driving transformative capabilities through technologies like machine learning, natural language processing, and computer vision. These tools enable systems to perform tasks with a level of efficiency and accuracy previously unattainable.
Machine learning algorithms empower systems to recognize patterns and make data-driven predictions without explicit programming. For example, they can analyze machinery temperature trends to forecast potential failures, enabling proactive maintenance. Likewise, computer vision enhances quality control by detecting defects in products with unparalleled precision and speed.
AI doesn’t just improve operational efficiency; it revolutionizes decision-making across all levels of an organization. Executives gain actionable insights through AI-driven data visualizations, shaping strategic plans. Meanwhile, factory operators receive real-time recommendations to streamline their daily activities. By democratizing information and insights, AI ensures that every stakeholder in the production chain plays a role in enhancing overall efficiency and achieving organizational goals.
Challenges and Future Directions
Despite their immense potential, AI-driven manufacturing systems face notable challenges. One primary concern is data security, as the interconnected nature of these systems introduces vulnerabilities that could be exploited if not properly safeguarded. Additionally, the integration of AI into legacy systems often demands substantial investments, both in financial resources and time, along with extensive training for the workforce to adapt to new technologies. However, the future holds immense promise. Fully autonomous factories, requiring minimal human intervention, are on the horizon. Furthermore, innovations like digital twins—virtual models of physical systems—could revolutionize predictive capabilities, enabling precise simulations and optimizing real-world implementations.
In conclusion, Deepak Bajaj’s work highlights that the marriage of AI with manufacturing heralds a new era of efficiency, sustainability, and innovation. Through smart factories and predictive maintenance systems, industries are not only addressing present-day challenges but also preparing for a future driven by intelligence and automation. This compelling exploration emphasizes the need for continuous exploration and adoption of AI in industrial domains. As the narrative unfolds, it’s clear that the intersection of technology and manufacturing holds unparalleled potential.
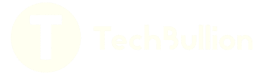