With its high competitiveness and rapid technological evolution, the manufacturing sector has seen significant advancements in recent years. One of the major contributors to this improvement is Carlos Macias, a highly sought-after engineer with over 20 years of experience.
Over the years, he has seamlessly integrated advanced technological solutions, particularly artificial intelligence (AI), into the traditional manufacturing processes.
“Manufacturing is transforming,” says Macias. “AI allows us to rethink how we approach efficiency, not just in speed but also in resource utilization, quality, and adaptability.”
He has helped companies optimize production, reduce waste, and cut costs by leveraging AI-driven solutions. For one, Macias developed an AI-driven maintenance scheduling system for a large-scale bus fleet in Bogotá. This system helped reduce maintenance costs and improve service reliability by minimizing unexpected disruptions. Macias has become a pioneer in AI-augmented mechanical engineering with his innovative approach.
“I help manufacturing companies in high-demand industries streamline their operations to make them more competitive on the global scale,” Macias shares.
Moreover, he doesn’t just focus on businesses; he finds it rewarding to see both businesses and people thrive: “I also work one-on-one with individuals, coaching them to achieve their goals in the manufacturing process,” he remarks.
In fact, during his career of over 20 years, this highly-regarded engineer showed his knack for nurturing talent. He identified promising yet inexperienced engineers and coached them to become high-performing Business Development Engineers.
Through Carlos’ personalized guidance, they developed skills in customer engagement, negotiation, deal-making, and technical expertise, including AI applications, accounting, and cost management. Through his efforts, his team was able to engage with major vehicle manufacturers like GM, Hino Motors, and Renault.
Merging AI with Mechanical Engineering
Macias’s journey into mechanical engineering began with his interest in precision and artistry. Growing up, he was fascinated by his neighbor, a mechanical engineer who spent long hours meticulously hand-drawing blueprints: “Watching him work with rulers, ink, and blades, correcting errors with a razor, made me realize that engineering was more than technical—it was an art form,” Macias recalls.
By the age of 16, he was already drafting mechanical designs. However, he had to juggle work (such as operating CNC machines) and technical school to fund his education. These experiences helped him blend theoretical knowledge with practical proficiency.
Over time, Macias got a degree from Universidad Autónoma in Cali, Colombia. He further sharpened his skill set with a specialization in Engineering Management Systems at Universidad Javeriana and an additional focus on Finance from Universidad Autónoma de Occidente.
While excelling in traditional manufacturing systems, Macias identified a critical shortfall – conventional methods often fell short in addressing the dynamic challenges of modern industries. This realization fueled his pursuit of innovative solutions to bridge traditional practices with the transformative power of AI.
“Traditional engineering relies heavily on static models and predefined rules,” Macias explains. “But the world isn’t static, and neither are manufacturing environments. That’s where AI comes in, allowing us to adapt in real-time.”
Macias uses machine learning algorithms and AI-driven tools to process vast amounts of factory-generated data as an industry expert. He empowers companies to make smarter decisions that enhance performance by uncovering inefficiencies and predicting potential bottlenecks.
One of his most notable projects involved implementing AI in a large-scale manufacturing facility to optimize production line workflows. By integrating sensor data from machinery with AI-driven analytics, his team identified inefficiencies costing the company millions annually.
“We reduced production time by 15% and cut energy consumption by 20%, all through adjustments that would have been impossible to spot without AI,” Macias says.
Gustavo Alberto Gómez, an industry veteran with over 30 years of experience in automotive manufacturing and process optimization, has collaborated with Macias on several projects. He has witnessed firsthand Macias’s transformative impact on the field and has nothing but praise for Macias’ skills.
“Macias is a rare talent in mechanical engineering,” he says. “Macias possesses a deep understanding of the automotive OEM landscape and consistently applies cutting-edge technology to meet industry-specific requirements.” He added that beyond his technical proficiency, Macias is committed to improving his work and helping others grow, which makes him a great asset to any team.
The Benefits of Smarter Manufacturing
Macias’ projects and previous works prove how artificial intelligence can take manufacturing processes to the next level, going well beyond minor, step-by-step improvements.
“AI doesn’t just make existing processes faster. It can redefine what’s possible,” Macias asserts. “With AI, we can predict machine failures before they happen, reduce material waste, and even personalize production at scale.”
One of his most impactful implementations involved predictive maintenance. By using AI to monitor machine performance, his team was able to predict breakdowns with over 90% accuracy, saving companies significant downtime and repair costs. “Predictive maintenance is a perfect example of how AI shifts us from reactive to proactive,” Macias explains.
As an industry expert, Macias played a key role in implementing the Reliability-Centered Maintenance (RCM) methodology for systems associated with industrial plants, reinforcing operational reliability in alignment with business objectives.
“The RCC is primarily a maintenance management tool,” Macias explained, “designed to maximize the operational reliability of assets within their specific operational context, based on a thorough analysis of actual maintenance requirements. I helped to implement a daily maintenance schedule for 800 buses in Bogota City with 99.8% accuracy of the operational schedule.”
With his unique expertise, Macias introduced an AI-powered vision system in a manufacturing plant in another project. Previously, workers manually inspected parts, a time-consuming process prone to errors.
The new system reduced inspection times to minutes and increased accuracy by generating 3D models to detect even minor deviations: “This not only saved time but also ensured higher-quality output,” he shares.
Being an expert in the field, Macias has proven leadership in driving cross-functional collaboration to achieve project goals using the Advanced Product Quality Planning (APQP) methodology. He has successfully led the Design Department, ensuring product development aligned with project objectives and customer requirements, delivering high-quality results and driving continuous improvement in manufacturing processes.
Challenges in AI-Driven Manufacturing
Macias acknowledges that integrating AI into manufacturing is challenging despite its immense potential: “The biggest hurdle is often cultural rather than technical,” he notes.
“Many organizations are hesitant to embrace AI because it requires a shift in mindset, from relying on traditional expertise to trusting data-driven insights.”
Macias recognizes that this cultural challenge often stems from the need to coach and develop people to adapt to new tools and processes: “In manufacturing, technology and machines are only part of the equation,” Macias emphasizes. “You also need skilled, motivated individuals who can connect data, machines, and workflows.”
To address this, he emphasizes the importance of education and collaboration. “Engineers and operators need to understand that AI isn’t replacing their expertise—it’s enhancing it,” he says.
“When people see how AI makes their jobs easier and more impactful, resistance tends to fade.”
Macias also emphasizes the need for substantial data collection and management practices. “AI is only as effective as the quality of the data it receives,” he warns. “Maintaining data accuracy and consistency should not be overlooked.”
Forging a New Horizon
Macias sees AI as a cornerstone of the future of manufacturing: “The factories of tomorrow will be fully connected ecosystems, where AI drives efficiency and supports sustainability and innovation,” he predicts.
Macias is particularly excited about the potential of AI to enable mass customization. “Imagine a world where factories can produce personalized products at the same speed and cost as standardized ones,” he says. “That’s the kind of transformation AI makes possible.”
Macias is equally passionate about the environmental impact of AI-driven manufacturing. “AI directly impacts sustainability by optimizing resource usage and reducing waste,” he explains. “It’s not just good for business; it’s essential for the planet.”
This sought-after expert’s dedication to sustainability complements his focus on continuous improvement in operational processes. Macias has judged numerous Kaizen teams on the Japanese method for incremental progress. This reflects his belief in the power of small yet consistent changes.
Carlos Macias: A Problem Solver at Heart
Macias thrives on solving problems. For him, every challenge is an opportunity to improve—whether by boosting efficiency, reducing costs, or creating groundbreaking solutions: “What excites me most about engineering is the chance to make things better, and AI takes that potential to an entirely new level,” he shares.
Collaboration is at the heart of Macias’s approach: “Engineering is a team effort,” he says. “The best outcomes come when we combine human creativity with the power of technology.”
Sandra Ochoa, Head of People and Strategy at IFAB Corporation, has witnessed the impact of Macias’s work firsthand. With extensive experience in operations management and process optimization, Ochoa has collaborated with Macias on several initiatives to enhance company efficiency and resource allocation. Sandra commends Macias for his contribution in transforming their process.
“Macias brought AI into our scheduling system, and it’s made a huge difference—better productivity, fewer mistakes, and smarter resource use,” Sandra recalls. “His ability to simplify processes, guide the team, and help us make better decisions has had a lasting impact on our operations,” she added.
Macias’ work shows how technology can transform industries. From predictive maintenance to supply chain optimization, his innovative solutions reshape manufacturing for a brighter, more sustainable future.
But for Macias, the key isn’t just technology- it’s people. He is passionate about teaching teams to bridge the gap between data, machines, and human decision-making.
“AI isn’t just about cutting costs or speeding processes,” Macias explains. “It’s about opening up new possibilities and ensuring manufacturing stays competitive and sustainable in this fast-changing world.”
His advice is to embrace change and never to be afraid of it. “Technology, especially AI, is not something to fear. It is a tool that can enhance our lives and businesses,” Macias explains.
Macias also highlights the importance of focusing on daily improvements and not stopping learning: “Focus on small, daily improvements, even just 1% better every day. You’ll be amazed at the results you can get over time.”
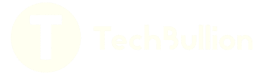