From powering pneumatic tools that drive nails and demolish concrete to inflating tires and operating paint sprayers, air compressors are the unsung heroes of construction sites, enabling a wide array of tasks that would otherwise be impossible or painstakingly slow.
In this in-depth exploration, we will delve into the multifaceted role of air compressors in the construction industry, highlighting their versatility, applications, and the undeniable benefits they bring to job sites of all sizes. We will also discuss important considerations such as choosing the right type of air compressor from the reputable Detroit air compressor company, proper maintenance, and safety protocols to ensure optimal performance and prevent accidents. Whether you’re a seasoned construction professional or a DIY enthusiast embarking on a home improvement project, understanding the significance of air compressors in construction can equip you with the knowledge needed to harness their power effectively and safely.
The Versatility of Air Compressors in Construction
One of the most prominent uses of air compressors in construction is to power a vast array of pneumatic tools. These tools, reliant on compressed air for their operation, are essential for a wide range of tasks. In demolition, jackhammers, chipping hammers, and other pneumatic demolition tools deliver powerful blows to break down concrete, asphalt, and other materials, making site preparation and renovation projects possible. For framing and carpentry, nail guns, staplers, and other fastening tools driven by compressed air dramatically speed up the process, boosting productivity and efficiency on the job site. Additionally, pneumatic drills and saws offer the power and precision needed to bore holes, cut through materials, and execute a variety of other essential tasks in construction. Finally, in the realm of painting and finishing, air-powered paint sprayers provide a smooth and even finish, saving both time and labor compared to traditional brush or roller application.
Beyond powering tools, air compressors also serve other functions on construction sites. They can be used to inflate tires on vehicles and heavy machinery, ensuring proper operation and safety. Additionally, compressed air is an effective tool for cleaning equipment, removing dust, debris, and other contaminants from surfaces and machinery.
Beyond the common uses we’ve discussed, air compressors also prove invaluable in various specialized construction tasks. In sandblasting, for instance, compressed air propels abrasive media at high velocities, effectively cleaning and preparing surfaces for painting, coating, or other treatments. Furthermore, air compressors are instrumental in pressure testing, where they pressurize pipes, tanks, and other systems to identify any leaks or weaknesses in their structural integrity, potentially preventing costly and time-consuming air compressors repair. In large-scale construction projects, air compressors often power concrete pumps, allowing for the efficient transportation and placement of concrete at elevated heights or in areas that are otherwise difficult to access.
Choosing the Right Air Compressor for Your Needs
The construction industry commonly utilizes several types of air compressors, each possessing its own set of advantages and ideal applications. Reciprocating compressors, for instance, employ pistons to compress air and are recognized for their robustness and adaptability, making them suitable for a wide range of construction tasks. These come in both portable and stationary models, catering to diverse needs on the job site. Rotary screw compressors, on the other hand, utilize rotating screws to compress air, and they generally operate more quietly and efficiently compared to their reciprocating counterparts. They find frequent use in continuous-duty applications or in environments where noise levels are a primary concern. Lastly, portable compressors, known for their compact size and lightweight nature, are perfect for construction sites where mobility is crucial. Typically fueled by gasoline or diesel engines, these compressors can be effortlessly moved to various locations as needed.
When selecting an air compressor, several factors should be considered:
Air Power Requirements: Determine the air pressure (PSI) and air flow (CFM) required by the tools and equipment you’ll be using. Choose a compressor that can deliver sufficient air power to meet your needs.
Tank Size: The size of the air tank determines how much compressed air can be stored. Larger tanks are suitable for applications that require a continuous supply of air, while smaller tanks may be sufficient for intermittent use.
Portability: If you need to move the compressor frequently, choose a portable model with wheels and handles.
Power Source: Consider whether you need an electric-powered compressor or a gas-powered one, depending on the availability of electricity at your job site.
Noise Level: If noise is a concern, opt for a quieter model, such as a rotary screw compressor or one with sound-dampening features.
Maintenance and Safety
Proper maintenance is essential for ensuring the longevity, efficiency, and safety of your air compressor. Adhering to the manufacturer’s recommended maintenance schedule is key. This typically includes tasks like regularly cleaning the compressor and its components, while also being vigilant for any signs of wear or damage. It also involves replacing air filters and oil as recommended by the manufacturer to ensure optimal performance and prevent contamination. Periodically draining the air tank to remove accumulated moisture, which can cause corrosion and affect air quality, is also crucial. Don’t forget to inspect belts and hoses for cracks, fraying, or other signs of wear, replacing them as needed.
For more complex repairs or maintenance tasks, it’s advisable to seek professional air compressor servicing from a qualified technician. They can diagnose problems, replace worn parts, and ensure that your compressor is operating safely and efficiently.
When operating an air compressor, everyone must follow safety guidelines to prevent accidents and injuries. Always wear safety glasses, ear protection, and gloves when operating the machine. It is crucial to avoid over-pressurization by ensuring that the pressure relief valve is functioning correctly and that the pressure gauge is accurate. Pneumatic tools should only be used for their intended purpose and in accordance with the manufacturer’s instructions. Handle compressed air with care, never pointing a compressed air nozzle at yourself or others. Finally, maintain a secure work area by keeping the space around the compressor clean and free of clutter. In the event of an air compressor malfunction or breakdown, it’s essential to have a plan in place. This may include having a backup compressor on hand or knowing where to find air compressors for rent in case of an emergency. If you experience a major issue, don’t hesitate to seek professional emergency air compressor repair to minimize downtime and ensure the safety of your job site.
Conclusion
Air compressors power lots of tasks and contribute to increased productivity, efficiency, and safety on job sites. By selecting the right air compressor for your needs, performing regular maintenance, and adhering to safety protocols, you can harness the power of compressed air while minimizing risks and ensuring optimal performance.
Whether you’re a construction professional or a DIY enthusiast, you have to understand the importance of air compressors and their safe operation. By following the guidelines and recommendations outlined in this article, you can make informed decisions about air compressor selection, maintenance, and safety, ultimately contributing to a more successful and secure construction experience. Remember, investing in a quality air compressor and prioritizing its upkeep can lead to long-term benefits, saving you time and money.
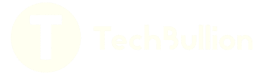