Teamcenter serves as a digital portal for accessing your organization’s product information, facilitating collaboration among all stakeholders requiring product and process expertise. Teamcenter facilitates the digital management of product and production data within the framework of the product lifecycle.
- Teamcenter enables all users within your worldwide business to access data in real time.
- Oversee product configuration.
- Regulate modifications to design and obtain approvals.
- Supply data to downstream applications, including enterprise resource planning (ERP) systems.
A Bill of Materials (BoM) is a detailed inventory that delineates the quantities, subassemblies, components, and raw materials necessary for the production or assembly of a finished product. Consider it a purchasing list or recipe for the production of a product. It functions as a fundamental document that directs the production process, guaranteeing that the appropriate materials are present at the appropriate time and location.
Engineering BOM and Manufacturing BOM
The eBOM is predominantly employed during the design and development phases of a product. It was developed by engineers and specifies the materials that are necessary in accordance with the initial design specifications. It furnishes details regarding the components, materials, and software that will comprise the final product. The eBOM is frequently employed as the foundation for the development of other forms of BOMs.
The mBOM is a more comprehensive extension of the eBOM, with an emphasis on the production process. Although the eBOM may include a bolt, the mBOM will specify its dimensions, material composition, supplier, and the quantity required for each unit of the final product. Typically, the mBOM serves as the primary source of information on the manufacturing floor.
Role of Structure Manager in Teamcenter
In Structure Manager, you establish a product structure, often referred to as a bill of materials (BOM). Teamcenter enables the visualization of an indented enumeration of the assemblies and components that constitute the product structure; the indentation facilitates the understanding of the relationships between the assemblies and components. An assembly has its own structure, while a component lacks structure.
Due to the potential disparity in life cycles between the assembly or component and the corresponding CAD design, Teamcenter allows for the independent management and release of the part and design. A single component may be represented by many CAD drawings, and conversely, a CAD design may pertain to numerous components. Alternatively, a site may maintain completely synchronized, identical component and design frameworks.
Part architectures are often designed for engineering change management and component reutilization. They may also be associated with ERP (enterprise resource planning) or other corporate systems. This differs from the CAD structures developed by design engineers, which are designed for component placement and reutilization.
In My Teamcenter, you may associate CAD design files, specification papers, or other information with the top-level assembly (the product) or with any assemblies or components.
Item components may also be attached to objects inside the product structure. They denote attributes that are not components of the physical structure but are related to or facilitated by it, such as weld sites or ports for connections. They are maintained as occurrence relations.
In Teamcenter, you may construct, visualize, and modify the product structure, or import it from CAD systems like NX and Mentor Graphics.
3D visualization data may be included as DirectModel dataset objects inside an item modification. Users may thereafter examine these photos inside the integrated viewer in Structure Manager.
Therefore, the Bill of Materials can managed with the Structure Manager, which has a wide range of capabilities.
A Bill of Material looks something like this on Structure Manager
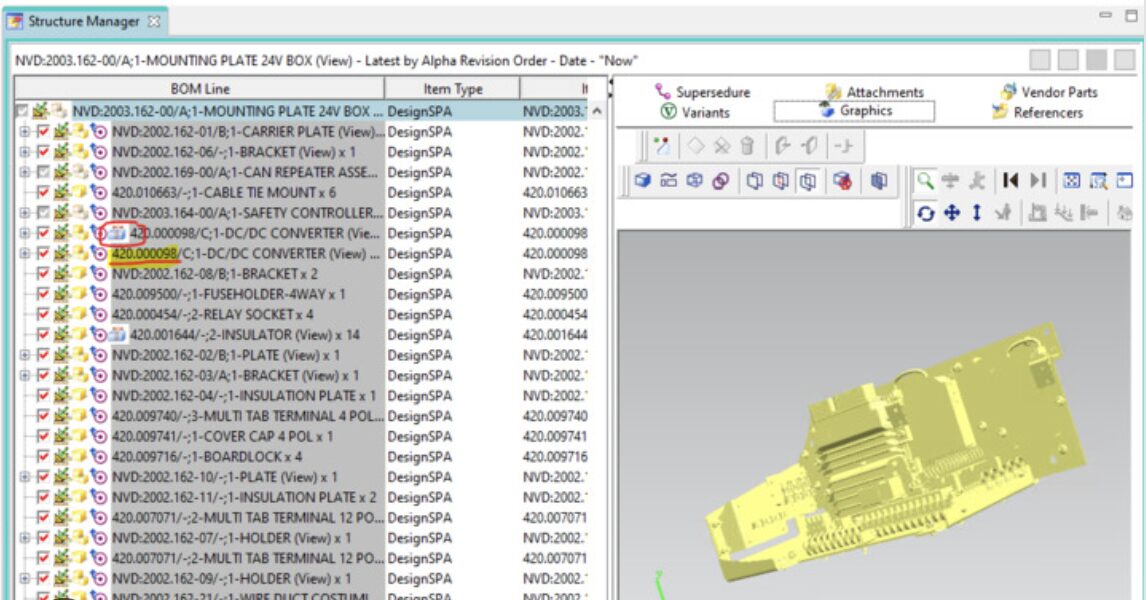
Credits: Siemens Communities
So, with this, we can see that assembly view tends to list all the parts that are required to manufacture the final product.
Impact of Variants in structure manager
Assume that a vehicle assembly is currently being put together. Consequently, this is the car model, denoted as X. Now, X can have numerous variants that are founded on the same design of model X but have subtly different features. The optimal solution is to employ the same assembly but offer a variety of options.
The Teamcenter Structure Manager provides an exceptional solution to this requirement, allowing for a variety of configurations. Variant configuration enables the creation of variants (e.g., color) and the specification of allowed values for each option. Afterward, you can associate these alternatives to a part.
For instance, you could establish a color option that permits only red and blue values. Variant configuration is typically implemented against a top-level assembly; however, it is feasible to implement them at any point within the structure.
You may then establish a variant condition on those occurrences in accordance with variant rules. A variation rule constitutes a collection of choices and values (e.g., color = red, material = steel) that is maintained inside the database. For instance, you may designate the load IF option color = value red inside the variation rule for the specified option and permissible values. To configure a certain variation of the assembly or product, it is necessary to establish the corresponding variant rule. To prevent users from designating invalid option values or combinations, default option values might be established, such as color = blue, inside the variation rule. Variant rule checks may also be established, such as an error if color equals green and substance is plastic.
From Concept to Creation: The Bill of Materials Journey
When the product production attains the eBOM phase, it indicates that it has successfully completed all initial approvals and CAD design stages.
- Specialists from several sectors, including engineering, procurement, manufacturing, and quality assurance, are engaged to provide their expertise. A cross-functional team guarantees the inclusion of all viewpoints.
- The process involves using product design documentation, blueprints, or CAD files to delineate all components of the final product. This constitutes the foundation of the BOM.
- A comprehensive inventory of all materials, parts, components, and subassemblies intended for the product is provided to guarantee that the eBOM encompasses them all. Technical requirements and other reference materials are meticulously reviewed for eBOM development.
- The exact amount of each component required to produce one unit of the completed product is assessed and computed.
- The design engineers then collaborate to convert the eBOM into the mBOM. At this juncture, the product cost and supplier information are also included into the data.
- Upon receiving approvals and all requisite certifications for the mBOM, the design is prepared for the shop floor. The mBOM is thereafter sent to the shop floor to begin production.
This summarizes the process from a Bill of Materials viewpoint; real product manufacture includes comprehensive workflows, approval procedures, changes, and certifications.
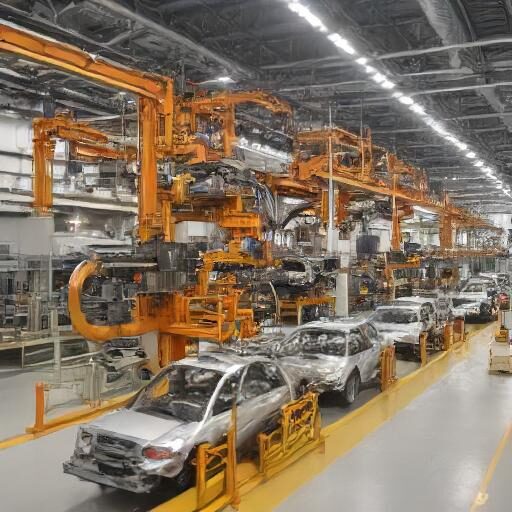
Credits: Siemens Communities
Reference:
[1] support.industrysoftware.automation.siemens.com, “Managing Prodocut Structure, Teamcenter 9”
[2] support.industrysoftware.automation.siemens.com, “Getting Started with Product StructureConfiguration: Configuring product structure with variants: Configuring product structure with variants” for Teamcenter 9.
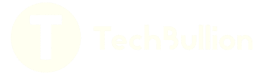