Laser cutting is a highly efficient and precise method for cutting various materials, including aluminum. However, achieving optimal results when laser cutting aluminum can be challenging due to its reflective and heat-conductive properties. This article provides six essential tips for improving your laser-cutting aluminum results.
Choose the Right Laser
Selecting the appropriate laser type is crucial for CNC laser cut aluminum effectively. Fiber lasers are generally preferred over CO2 lasers for cutting metals, including aluminum, because of their wavelength and efficiency.
Fiber lasers operate at a shorter wavelength (typically around 1 µm) compared to CO2 lasers (10.6 µm), which allows for better absorption by the aluminum. This results in more efficient cutting with less reflection and higher precision. For example, a 1 kW fiber laser can cut aluminum more efficiently than a CO2 laser of the same power.
The power of the laser also plays a significant role. Higher-power lasers can cut thicker aluminum more efficiently. For instance, a 4 kW fiber laser can cut up to 10 mm thick aluminum with high precision. It’s also important to match the laser power to the specific application to avoid unnecessary energy consumption and potential damage to the material.
Optimize Laser Parameters
Adjusting laser parameters such as speed, power, and focus can significantly impact the quality of the cut. A fast cutting speed can result in complete cuts or poor edge quality, while too slow can cause excessive melting and rough edges. Finding the optimal speed for the specific thickness and type of aluminum is essential. For instance, cutting 1 mm aluminum might require a speed of around 6000 mm/min, while 10 mm aluminum might need a speed closer to 1000 mm/min.
The laser power needs to be set according to the thickness of the aluminum. For example, cutting 3 mm thick aluminum may require around 1 kW of laser power, whereas cutting 10 mm thick aluminum might require 3-4 kW. Adjusting the power settings appropriately ensures clean cuts without excessive burrs or thermal damage.
Proper focus is critical for a clean cut. The focus position should be adjusted to concentrate the laser beam on the aluminum surface precisely. Misalignment can lead to poor edge quality and increased kerf width. Auto-focus systems help maintain consistent focus during cutting, especially for complex geometries.
Use Appropriate Assist Gas
The type and pressure of the assist gas used during laser cutting can influence the quality and speed of the cut. Nitrogen and oxygen are commonly used gases for cutting aluminum.
Nitrogen is often preferred for cutting aluminum because it produces a cleaner cut without oxidizing it. Oxygen can increase cutting speed but may cause oxidation and affect the surface finish. For instance, high-pressure nitrogen can help achieve a bright, oxide-free cut edge on aluminum.
The pressure of the assist gas should be optimized for the best results. High-pressure nitrogen can help remove molten material from the cut zone more effectively, leading to smoother edges. For example, cutting 6 mm thick aluminum might require nitrogen at 10-12 bar pressure. The optimal gas pressure can vary depending on the thickness and desired cut quality.
Minimize Reflectivity Issues
Aluminum’s high reflectivity can pose challenges during laser cutting by reflecting the laser beam away from the cutting area.
Applying anti-reflective coatings to the aluminum surface can help reduce reflection. These coatings absorb some of the laser energy, making cutting more efficient. Specialized anti-reflective coatings can be applied to the material before cutting or integrated into the laser system optics.
Polarized laser beams can also mitigate reflectivity issues. Polarized beams are less likely to be reflected away from the cutting surface, resulting in better energy absorption and cutting performance. Beam polarization techniques, such as quarter-wave plates, can be implemented in the laser system to enhance cutting efficiency.
Modern laser systems often incorporate protective measures like sensors and feedback mechanisms to detect and compensate for reflected laser energy. These measures help protect the laser source and maintain cutting efficiency.
Ensure Proper Material Handling
Proper handling of the aluminum sheet before and during the cutting process can prevent issues such as warping and inconsistent cuts. Ensure the aluminum sheet is flat and free of bends or warps. Warped material can cause the laser to lose focus and result in uneven cuts. Using a vacuum table or clamps can help keep the material flat. Automated handling systems can also load and position aluminum sheets accurately on the cutting bed.
Any contaminants on the aluminum surface, like oil, grease, or dirt, can affect the cutting process. Clean the aluminum thoroughly before cutting to ensure consistent results. Solvents or specialized cleaning agents can help effectively remove surface contaminants.
Automated material handling systems can improve consistency and reduce manual errors. These systems can include features like automated loading, unloading, and alignment to enhance the overall efficiency of the cutting process.
Implement Cooling Techniques
Aluminum’s high thermal conductivity can lead to heat buildup during cutting, affecting the quality of the cut and potentially causing thermal distortion.
Active cooling methods, such as water and air cooling, can help dissipate heat more effectively, reducing the risk of thermal distortion and improving cut quality. Active cooling systems can be integrated into the laser-cutting machine to maintain optimal operating temperatures.
Plan your cutting path to manage heat distribution effectively. Avoid cutting too many intricate patterns in a small area, leading to localized heat buildup. Spacing out the cuts and allowing for cooling periods can help maintain the quality of the cuts.
Emerging technologies, such as cryogenic cooling, are being explored to enhance the cooling process during laser cutting further. These techniques involve extremely low temperatures to minimize heat-affected zones and improve cut quality.
Conclusion
Improving aluminum’s laser cutting results involves carefully considering various factors, from choosing the right laser type to optimizing laser parameters and managing reflectivity issues. Implementing these six tips can achieve high-quality, precise cuts on aluminum. They will not only enhance the efficiency of the cutting process but also contribute to the overall quality and consistency of the final product.
Read More From Techbullion And Businesnewswire.com
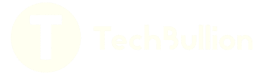