Zirconia ceramics possess an array of mechanical, thermal and chemical properties. Their mechanical strength includes high flexural and tensile strengths as well as toughness characteristics.
Dependent upon its stabilizer (yttria or ceria), different varieties of zirconia excel in environments in which metals, plastics and ceramic materials cannot. This has made zirconia the go-to material in numerous applications and industries worldwide.
High Strength and Toughness
Zirconia stands out as an exceptional ceramic material today due to its incredible toughness and fracture resistance, which make it one of the strongest materials currently available. These properties allow it to perform in operating environments where plastics and metals simply don’t excel such as high temperature environments and abrasion; making it the material of choice for applications ranging from high altitude aircraft components to surgical tools and prosthetics.
Zirconia ceramics possess high fracture toughness due to both their microstructure and stabilizer content. Stabilizers like yttria, magnesium oxide and cerium oxide help prevent its crystal structure from changing under stress while strengthening strength and thermal shock resistance of this ceramic material.
Zirconia comes in three main crystalline forms, monoclinic, tetragonal and cubic. To strengthen tetragonal zirconia’s thermal tolerance and fracture toughness (also referred to as transformation toughness), Yttria stabilizes it by producing metastable forms with increased fracture toughness; by changing from tetragonal to monoclinic it causes volume increases that close cracks while strengthening material.
Engineering ceramics may provide similar fracture toughness ratings, but few provide comparable performance to zirconia. International Syalons’ Zircalon 5 has an exceptionally high fracture toughness rating of 8.0 MPa m 1/2; our yttrium oxide stabilized zirconia Zircalon 10 outshone this performance even further with 10.0 MPa m 1/2 fracture toughness ratings.
High Thermal Conductivity
Zirconia ceramics stand out from other ceramics by their ability to withstand high temperatures. Due to this feature, along with durability and chemical resistance, zirconia ceramics have become popular choices for hip replacements as well as for cladding industrial fuel rods. Furthermore, zirconia ceramics also exhibit exceptional fracture toughness and hardness at room temperatures – making them perfect materials for hip replacements and industrial fuel rods cladding applications.
Zirconia ceramics can be formed into various shapes, sizes and structures for diverse applications. They can be machined, welded or adhered directly onto other materials – offering great versatility when it comes to shaping them to meet specific needs.
Research is ongoing to improve zirconia ceramics strength and toughness by exploring novel processing techniques and additives, while scientists also seek methods of increasing its thermal conductivity for specific applications.
Stabilized with yttrium oxide (Y) into 8 YSZ, zirconia exhibits outstanding corrosion, fracture toughness, and thermal shock resistance. The addition of Y changes its monoclinic phase into tetragonal and cubic polymorphs with higher thermal expansion rates; only oxygen ions pass through this material.
8 YSZ’s unique properties make it an excellent material for dental implant abutments and crowns, but grinding the material may activate a low-temperature degradation process known as “yttrium aging,” producing yttrium hydroxide in water-filled environments and diminishing microcrack resistance and strength over time. Yttrium aging poses particular threats for metal frameworks exposed to oral environments as well as components not coated in ceramic veneer.
Excellent Corrosion Resistance
Zirconia ceramics are highly corrosion-resistant due to the fact they can be manufactured through non-melting methods. Zirconia can also be shaped into components with tight tolerances and easily bonds with materials such as titanium, steel, glass and composites.
Zirconia has proven itself an exceptional material for medical applications like dental implants. When compared with alternatives like stainless steel, zirconia stands out with superior durability and longevity compared to its competition. Furthermore, zirconia is biocompatible – meaning that its presence won’t harm human tissue.
Stabilized zirconia outshines unstabilized materials in terms of toughness, hardness and thermal conductivity due to a process used during production that prevents and controls structural changes caused by exposure to high temperatures. Oxides such as yttria, ceria, magnesia and alumina are commonly added during this stage in order to safeguard and strengthen its structure and improve performance.
Yttria stabilized zirconia (YTZP), consisting primarily of the tetragonal phase, is often utilized in demanding mechanical applications due to its superior performance characteristics. It does not experience phase transformation at higher temperatures that is common with unstabilized zirconia, has an heterogeneous microstructure that helps inhibit grain boundary sliding, and is toughened through transformation to resist crack propagation.
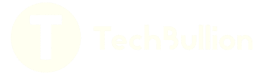