Input and output modules, or I/O modules, are the essential bridge between the “brain” of an industrial control system (often a PLC) and the real-world devices that make things happen. They act as the system’s eyes, ears, and hands, translating sensor readings and control signals into a language the PLC can understand and act upon.
Input Modules: The “Senses” of Your System These modules gather data from the physical world. They convert signals from various sensors like:
- Proximity Switches: Detecting the presence or absence of objects
- Limit Switches: Signaling mechanical limits and positions
- Temperature Sensors: Monitoring process temperatures
- Pressure Transducers: Measuring fluid pressures
Output Modules: The “Muscles” of Your System These modules carry out actions based on commands from the PLC. They control devices like:
- Motor Starters and Contactors: Starting and stopping motors
- Solenoid Valves: Controlling the flow of fluids or gasses
- Process Control Valves: Precisely regulating flow rates
- Indicator Lights and Alarms: Signaling system status
Why I/O Modules are Key:
- Centralized Intelligence: I/O modules allow you to connect numerous sensors and actuators throughout a facility to a centralized PLC. This enables sophisticated control logic and decision-making based on real-time information.
- Signal Conditioning: Many raw sensor signals are unsuitable for direct connection to a PLC. I/O modules handle voltage conversions and filtering and sometimes even provide isolation to protect the PLC.
- Modularity and Flexibility: I/O modules come in many types and channel counts. This allows you to tailor your system precisely to your application’s needs and adapt as those needs change over time.
Think of I/O modules as the essential translators that enable your PLC to perceive and interact with its environment, ultimately governing your automated process or industrial machine.
Types of Input Modules
Input modules are tailored to handle the diverse range of signals they encounter in the industrial world. Let’s explore the main categories:
Digital Input Modules
These are the workhorses for detecting discrete, on/off states. They interface with pushbuttons, limit switches, and proximity sensors that provide a simple open or closed contact. Digital input modules excel at presence/absence detection, basic counting, and monitoring equipment status.
Analog Input Modules
Where digital inputs are all-or-nothing, analog input modules bring nuance by measuring continuous signals for greater precision. They are essential in handling sensors that output variable voltage or current signals (like 0-10V or 4-20mA), representing process values like temperature, pressure, or flow rate. Analog input modules allow the control system to make fine adjustments or react to gradual changes in a system.
Specialty Input Modules (Thermocouple, RTD, etc.)
Certain sensor types require specialized input modules for proper signal processing. Consider these examples:
- Thermocouple Modules: Designed for the unique, low-voltage signals thermocouples produce. They often feature built-in temperature compensation for accurate readings.
- RTD Modules: Optimized for Resistance Temperature Detectors (RTDs), which sense temperature changes based on electrical resistance. These modules sometimes provide the excitation current needed by RTDs.
- High-Speed Input Modules: Some applications, like fast counting or encoder feedback, demand input modules with extremely fast response times to capture events accurately.
Important Point: When selecting input modules, ensure signal type compatibility (voltage vs. current, digital vs. analog, etc.) and match any specific requirements your sensors might have.
Types of Output Modules
Just as input modules handle diverse signals coming in, output modules are specialized to drive many devices on the plant floor. Let’s look at the major categories:
Digital Output Modules
Similar to digital input modules, these deal with on/off control. They convert PLC commands into appropriate voltage levels to energize solenoids, turn on indicator lights, trigger motor starters, or activate other simple on/off devices.
Analog Output Modules
Analog output modules provide the finesse for proportional control. They generate variable voltage or current signals (such as 0-10V or 4-20mA) that instruct devices like variable frequency drives (for motor speed control), proportional valves (for precise flow regulation), and process instrumentation displays.
Specialty Output Modules (Relay, etc.)
Some common devices demand specific output types:
- Relay Output Modules: These offer electromechanical switching via internal relays. They are useful for switching higher currents or voltages than a standard digital output can handle or when electrical isolation is required.
- Pulse-Width Modulation (PWM) Outputs: These modules generate rapid on/off pulses to control devices like dimmable lights or DC motor drives. The pulse duty cycle determines the average output power.
- Specialized Motion Control Outputs: Modules for complex motion tasks might output high-speed step/direction pulse trains for stepper motors or communicate directly with servo drives via industrial protocols.
Key Consideration: When choosing output modules, it’s vital to ensure that the module’s voltage, current rating, and switching type (sink vs. source) are compatible with the devices you’ll be controlling.
How to Choose the Right Input and Output Modules
Selecting the most suitable I/O modules for your industrial automation project requires careful consideration of several factors. Here’s a roadmap to guide your decision-making:
- System Requirements:
- Signal Compatibility: This is paramount. Ensure your I/O modules match the signal type your sensors or actuators produce (voltage vs. current for analog, open/closed contact for digital).
- Number of Channels: Count the sensors and actuators you need to connect. Choose modules with the appropriate channel count to avoid unnecessary expense or the need for multiple modules.
- Communication Protocol: Consider how the I/O modules will communicate with your PLC. Popular options include digital protocols like Modbus, Profibus, or even industrial Ethernet.
- Application Specifics:
- Environmental Conditions: Will your I/O modules be exposed to extreme temperatures, vibration, or moisture? Choose modules with appropriate enclosure ratings (NEMA) to ensure reliable operation.
- Safety Considerations: Are there any safety-critical functions involved? Some applications require modules with specific safety certifications (SIL ratings) for fault tolerance.
- Future Expansion: Consider if you need to add more sensors or actuators in the future. Modular I/O systems that add additional modules later can be wise investments.
- Additional Considerations:
- Power Supply Requirements: Ensure your power supply can handle the combined current consumption of all the I/O modules you choose. Consult the manufacturer’s specifications for power consumption per channel.
- Physical Size and Mounting: I/O modules come in different sizes. Factor in space constraints within your control cabinet and choose modules that can be mounted securely.
- Manufacturer Reputation and Support: Partner with a reliable I/O module supplier that offers technical support and ensures compatibility with your chosen PLC platform.
You can select I/O modules that perfectly match your application’s needs by carefully evaluating these points. Feel free to consult with automation specialists or the I/O module manufacturer if you have any questions during the selection process.
Applications of Input and Output Modules
Input and output modules are the backbone of countless automated systems across diverse industries. Here are a few key sectors and some illustrative examples:
Manufacturing
- Assembly lines: Input modules monitor part presence sensors, conveyor encoders, and process equipment status. Output modules control motors, valves, and indicators for a coordinated production flow.
- Bottling/Packaging: Ultra-fast input modules count products or detect labels. Output modules accurately trigger filling valves or divert packages based on sensor readings.
- Robotics: Input modules handle robot encoder feedback, proximity detection for workpieces, or safety interlocks. Output modules command servo motors and control grippers or process tools.
Process Industries
- Chemical Processing: Analog input modules monitor temperature, pressure, flow, and tank level sensors. Output modules precisely control valves and pumps for accurate mixing and batch control.
- Water/Wastewater Treatment: Input modules manage treatment plant instrumentation. Based on sensor readings, output modules activate pumps, aerators, and chemical dosing systems.
Building Automation
- HVAC: Input modules handle temperature and occupancy sensors for comfort control. Output modules regulate heating/cooling elements, fans, and motorized dampers.
- Lighting Control: Input modules interface with photosensors and occupancy detectors. Output modules dim lights, control smart ballasts, and activate lighting relays based on need.
Transportation and Logistics
- Conveyor systems: Input modules detect packages with photoelectric sensors for sorting. Output modules control diverters, motors, and signal lights.
- Warehouse Management: RFID systems use specialized input modules for tag reading, while output modules trigger sorting devices or control inventory robots.
This is just a glimpse! I/O modules are found in automated agriculture, power generation, pharmaceutical production, and countless other fields where precise control and data acquisition are necessary.
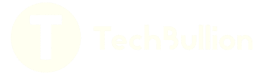