Industrial valves play a crucial role in regulating the flow of fluids and gases in various processes. From controlling water flow in a municipal water treatment plant to managing oil flow in a refinery, valves are essential components of industrial systems. However, like any mechanical component, valves can experience problems that may disrupt operations. In this user-centric technical article, we will explore common valve problems encountered in industrial settings and provide practical solutions to address them.
Common Valve Problems
- Leakage: Valve leakage is a prevalent issue resulting from damaged seals or improperly closed valves. It can lead to fluid loss, environmental hazards, and compromised system efficiency.
- Blockage: Blockages can occur due to debris or contaminants in the fluid. When valves become blocked, they impede the flow of the substance, causing reduced efficiency and potential damage to the valve.
- Sticking: Sticking valves do not open or close as they should, often due to insufficient lubrication, corrosion, or foreign particles. This problem can disrupt the process they control.
- Corrosion: Corrosion is a persistent issue in industrial settings, and valves are not immune. It can deteriorate valve components, leading to leaks, blockages, or sticking.
- Noisy Operation: Valves may produce excessive noise during operation, which disrupts the workplace and can indicate underlying issues like cavitation or damaged components.
Identification and Troubleshooting
Early detection and correction of these problems can help ensure your valves’ safe and reliable operation. Here are some tips to help you identify and address common valve problems:
- Leakage Identification: To identify valve leakage, look for visible signs of dripping, staining, or puddles around the valve. You can also use leak detection solutions or ultrasonic equipment to detect leaks that are not immediately visible.
- Blockage Detection: Regular inspections can help spot blockages. If you suspect a blockage, shut off the valve and remove it for cleaning. Ensure the fluid is free of contaminants before reinstalling the valve.
- Sticking Valve Diagnosis: Sticking valves often require disassembly and inspection. Look for signs of corrosion, foreign particles, or inadequate lubrication. Clean and lubricate the valve components to resolve sticking issues.
- Corrosion Inspection: Corrosion can be visible on valve surfaces. Regular inspections are vital to catch corrosion early. You can prevent corrosion by selecting materials resistant to the process fluid and applying protective coatings.
- Reducing Noise: Consider installing noise-reducing accessories or modifying the valve’s design to address noisy valves. The noise may also be a symptom of other issues, so thorough inspection is crucial.
Preventive Maintenance
Preventive maintenance is key to avoiding common valve problems.
- Select the right valve for the application: It is important to select a valve designed for the application’s specific fluid type, pressure, and temperature conditions.
- Install the valve properly: Valves must be installed according to the manufacturer’s instructions to ensure proper operation.
- Perform regular maintenance: Valves should be inspected and maintained on a regular basis to identify and address potential problems early.
- Regular Inspection: Regularly inspect valves for signs of wear, damage, or leaks. Address issues promptly to prevent them from escalating.
- Lubrication: Proper lubrication can prevent sticking and reduce wear. Follow the manufacturer’s recommendations for lubrication frequency and type.
- Temperature Control: Maintaining the right operating temperature can help prevent issues like blockages and sticking, especially in processes involving temperature-sensitive fluids.
- Use a valve management system: A valve management system can help track valve maintenance schedules and identify valves that are at risk of failure.
Conclusion
Valves are indispensable in industrial settings but are not immune to problems. Understanding common valve issues, their identification, and troubleshooting methods are essential for maintaining efficient operations. By practicing preventive maintenance and promptly addressing issues, you can ensure that your valves perform optimally and contribute to the overall success of your industrial processes.
Resource
Figure 1: https://tameson.com/products/bw3-100-aw1-024dc-electric-ball-valve-1inch-3-way-24vdc-3-point
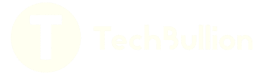