In today’s rapidly evolving industrial landscape, the electric motor has undoubtedly become the most prevalent mechanical power source in modern manufacturing environments. However, it is imperative to recognize that while electric motors offer numerous advantages, they may not always be the optimal or safest choice for every application. Industry 4.0 has ushered in an era of digitalization and electrification in manufacturing processes and assembly tools, where electric motors have taken center stage due to their impressive energy efficiency and the increased operational flexibility they afford to factory floor operators. Furthermore, advancements in battery technology have eliminated the need for cumbersome power cords, enhancing the mobility and versatility of electric motor-driven tools. These innovations have undoubtedly reshaped the industrial landscape, but they do not signify a one-size-fits-all solution.
In certain industrial manufacturing environments and specific applications, the venerable air motor, powered by compressed air, emerges as the superior alternative. Over the past two centuries, industrial manufacturers have relied on air motors to energize handheld and fixture tools, and years of relentless improvements and developments have propelled air motors to the forefront, offering unparalleled safety, operational efficiency, and cost benefits.
Safety always takes precedence in industrial manufacturing environments, and air motors have a unique ability to excel in delicate manufacturing settings. They avoid overheating and sparking, significantly mitigating the risks of fires and explosions, making them indispensable in scenarios where safety is paramount.
Another remarkable attribute of air motors is their outstanding power-to-weight ratio, which surpasses that of electric motors by a factor of 2-3. This exceptional ratio, combined with the ability to operate in any position, positions air motors as the ideal choice for applications that demand both flexibility and power. Whether it’s reaching tight spaces or handling heavy loads, air motors deliver unmatched performance.
Moreover, air motors stand out for their ability to maintain consistent operation even at high cycle rates. Unlike electric and battery-powered tools, which necessitate vigilant heat monitoring to prevent damage, air motors remain cool and reliable through cooling via air expansion. This longevity and reliability contribute significantly to enhanced manufacturing productivity.
Furthermore, air motors boast cost advantages with lower installation and maintenance expenses, translating to reduced total cost of ownership. These economic benefits further enhance their attractiveness as a choice for budget-conscious manufacturers.
In conclusion, while electric motors have undeniably revolutionized modern manufacturing with their energy efficiency and operational flexibility, it is essential to recognize that the air motor, driven by compressed air, is the superior choice in certain applications. To make an informed decision, manufacturers should carefully assess their specific needs, taking into account safety requirements, power-to-weight ratios, operational flexibility, and total cost of ownership. Exploring the range of offerings from Atlas Copco, which includes both air motors and electric motors, allows for a tailored approach that aligns with the unique demands of each manufacturing operation. Whether it’s the versatility of electric motors or the reliability and safety of air motors, the right choice will ultimately enhance productivity and safety in the industrial manufacturing environment.
Learn more about the Atlas Copco air motors and electric motors to choose the right product for your needs.
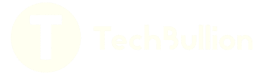