There is enough debate on CNC, of which so much industrial feedback goes in its favor. And how come it can’t go right? Big manufacturing firms, from medical to big heavy machinery manufacturing industries, have utilized its benefits for many years since its invention fifty years ago. Since then, it quickly gained much acceptance and applause.
Today, we’re exploring CNC parts but in a much greater degree of detail. We have gathered all the information from reputable sources, so you don’t have to. Just read our article, which has everything you need to know about CNC machining parts.
What defines CNC machine parts?
A simple science, precision-machined part will have the same dimensions across many components. That’s why when you go to a machine shop, they come up with a perfect tool/product that meets your precision requirements, which also means that they can meet them for multiple parts of the same design.
This ability to meet these requirements also means that a shop is more likely to meet your design’s accuracy targets/tolerance requirements – however, technically, a machine shop can reach high precision without ever meeting accuracy requirements.
CNC Machining parts: Everything you need to know
You should know the 13 key Cnc machining parts since they’re complex assemblies with many parts. These key components fall into two categories: (a) control system and (b) machine system.
1. A control system (CS)
In CNC machines, the control system controls information, inputs, and outputs. A control system consists of:
- Control panel
- An input device (a tape reader, magnetic tape reader, or an RS-232-C port) is needed.
- A machine control unit (MCU) is responsible for controlling the machine.
- Input/output feedback
They work together to let the machine and humans create parts accurately. MCUs take inputs from control panels and input devices and convert them into machine commands. Transducers and sensors do real-time measurements of the cutting tool’s position and speed. After that, the MCU listens to the feedback and makes adjustments.
2. Machine System
A machine system manipulates and shapes a workpiece into the finished product. There are several critical components to the machine system, including:
- Driving system: Driving systems move workpieces with lead screws and motors.
- Machine tool: Workpieces and machine tools move, and the machine tool cuts away the material.
- Headstock: Headstock is crucial to the turning process, which involves shaping cylindrical objects. It holds and rotates the workpiece to create symmetrical shapes. It’s great for making shafts, bushings, and other rotational parts.
- Spindle: CNC spindles serve mainly two purposes: – Maintain constant power within a certain speed range so that cutting force is enough. The spindle can be positioned accurately to change tools, withdraw boring tools, and do other things. Taping simultaneously
- Chuck: For holding the workpiece steady, the headstock has chucks that hold it in place.
- Tool turret: CNC machines can automatically swap tools via turrets or automatic tool changers.
- Tailstock: Tailstocks are used to minimize deflection when machining long workpieces.
- Coolant tank: A coolant tank pumps coolant into the machined part to prevent it from getting damaged by the intense heat generated during machining.
- Machine bed: The CNC machine bed provides structural support to all these components.
CNC Machines: How Do They Work?
There’s a lot of engineering behind Cnc machining parts. Combined with all these components, a reliable, high-quality machine is built with minimal operator input. The question is, how? The answer to this question is explained comprehensively below.
1. Reading a program
The input device reads A program into the CNC machine’s machine control unit (MCU). The program contains all the instructions needed to produce a specific part. It tells what tool to use, how fast, where, and anything else it needs to know.
Over the years, how the program is read into the MCU has changed greatly. Initially, NC (numerical control) machines worked by punching holes in paper tape. As digital technology evolved, CNC was born, allowing programs to be read digitally. Usually, CNC machines use G code and M code to feed programs into them to keep them portable.
2. Putting the program into action (Execution part)
The motion system receives commands from the MCU as part of the making process. CNC machines have motors, pumps, and solenoids and are more controlled by the MCU.
The MCU is the machine’s brain, telling all its components what to do and when to do it.
3. Getting rid of errors
The ability to correct errors is what makes CNC machines so powerful. Using a feedback unit, the MCU measures the position and velocity of the machine tool.
By comparing the requested output to what the feedback unit measures, the MCU updates the outputs to the motion system accordingly – minimizing errors.
CNC Turning Machine Components
Let’s review the most commonly used CNC machine for a case study to get a clearer perspective. A turning machine has a spindle attached to the machine drive system at one end, and a chuck grips the workpiece at the other. There are typically three or four jaws on a chuck, with three jaws being the most common. You can use four-jaw chucks to turn square bars off-center and grip square bars.
Carbide inserts are commonly used in cutting tools. Depending on the tool, the inserts go in tool holders, bolted to the turret using specialized holders. In preparation for machining, tools are indexed.
CNC Turning Tooling Materials
Several companies research better inserts, coatings, and alloys to boost tool life and performance. Inserts come in different designs, so choosing one appropriate for the machined material is important. It’s easy to break a tool or damage the workpiece if you try to machine a hard material with a tool meant for softer materials.
Crystal orientation is a big part of materials engineering for CNC turning tool inserts. The grains in a material can be analyzed through magnified images taken through a microscope. These grain sizes, shapes, and orientations depend on the material composition (alloy) and how it’s made or modified (heat treatments, etc.). The grain sizes and orientations affect mechanical properties.
A unidirectional crystal structure helps the cutting edge stay in shape longer, improves wear resistance, and extends tool life.
Here’s a breakdown of the different types of CNC machining operations
The term “turning” is used to describe a variety of operations that can be performed on a turning center. There are several types of turning, including:
Orienting:
It’s the process of cutting a flat surface perpendicular to a workpiece’s rotational axis. In the lathe, the tool is mounted in a tool holder.
Faceting tools feed perpendicular to the part’s rotational axis during the process. It can be done as a roughing cut or as a final pass.
Turning:
Turning is when a CNC machine removes material from the outer diameter of a part. Tapered parts can be turned parallel to the rotational axis or at an angle.
Drilling:
The drill is used if the hole is on the rotational axis of the part. A hole can be drilled almost anywhere, not just in the center axis on more advanced turning centers.
Boring:
It’s sometimes necessary to enlarge holes after they’ve been drilled. An easy way to do that is to bore a hole and remove material from the inner wall by feeding the cutting tool into it.
Threading:
The threading process involves cutting threads into holes or over a workpiece’s outer diameter.
Partitions and grooves:
Typically, grooves are used to make features like O-rings and circlips. Grooving tools are used to remove the finished part from the workpiece stock.
FAQs
What are the basics of CNC?
The CNC (Computer Numerical Control) machine makes a custom-designed part using computerized machine tools. When chipping away (removing) a material, a computer uses programming codes. The material won’t form the input designed part until it’s processed.
What is the main part of the CNC machine?
CNC machines are composed primarily of a headstock. To finish the job, the workpiece is mounted on the headstock. The main spindle motor is also on this part. The tailstock gives you extra grip when threading or knurling your workpiece.
What are the Main Components of a CNC Milling Machine?
CNC milling is the most frequently used milling machine due to obvious reasons. Its main parts include a frame, spindle, axes, columns, a CNC control panel, and other important parts.
Conclusion
In this series of explanations, we explored CNC’s machining parts to a much greater extent. The main focus was to get all the important insights into the technology. It’s helpful for industrialists who are just thinking of implementing CNC, but it is also very beneficial for people interested in the field.
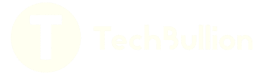