Introduction:
Welding produces harmful fumes containing toxic gases and metal particulates that can lead to long-term respiratory illnesses. Having proper fume extraction is crucial for any welding workspace to protect the health and safety of welders. This in-depth guide covers the key types of welding fume extractors, important features to look for, installation and usage tips, and maintenance best practices.
What Are Welding Fume Extractors and Why Are They Important?
Welding fume extractors are ventilation systems engineered specifically to capture welding smoke and fumes right at the source before they spread into the surrounding environment. They work by pulling the contaminated air through a filter and then venting the cleaned air back out. There are portable models for small spaces and stationary installs for larger fabrication shops and multiple welders. Using a suitable fume extractor improves air quality, reduces exposure to dangerous metal particulates, increases weld visibility, minimizes fire risk, and keeps the workspace compliant with occupational health standards. Protecting welder’s respiratory systems from the tiny toxins and gases released during welding should be a top priority for any shop.
Choosing the Right Type of Fume Extractor
There are several key considerations when selecting the right fume extraction solution:
- Size of workspace – Small portable extractors are better for tight spaces with one welder versus stationary models with higher capacity for larger shops. Evaluate the work area and number of welders needing coverage.
- Portability needs – If needing to move around the workspace, wheeled portable extractors offer better flexibility. Stationary mounts provide fixed installation.
- Extraction direction – Back draft pulls fumes away from welder’s face versus downdraft drawing fumes down. Consider the setup and welder positioning.
- Filtering – Ideally filters are multi-stage to effectively trap particles. They should also be easily accessible for routine cleaning and replacement.
- Automatic operation – Look for auto-on when arc welding starts and adjustable timer shutoff afterwards. This ensures it runs only when needed.
- Noise level – Choose quieter fans and motors if noise is a concern in your environment.
- Durability – Seek robust outer materials like powder coated steel to withstand potential shop abuse. Internal components should also be protected.
Key Features to Look for in Fume Extractors
Beyond the type, there are several key performance features and extra capabilities to look for:
- High airflow CFM rating – This determines fume capture power. Look for at least 100 CFM per active welding station.
- Variable speed control – Allows adjusting suction power to suit the welding task.
- Self-cleaning function – Some models include automatic filter cleaning mechanisms via pulsing air flow.
- Automatic sensors – Sensors detect when welding starts/stops to control operation only when needed.
- Remote controls – Allows starting, stopping or setting adjustments from a distance. Helpful for stationary units.
- Alarm indicators – Alert user if filter needs replacement or other maintenance required.
Installation Tips for Optimal Fume Extractor Positioning
Proper installation positioning is vital for fume extractors to adequately capture the released gases and particulates. Here are some recommendations:
- Mount as close as possible – Try to position extractor nozzle 18-24 inches from weld zone to effectively capture fumes.
- Angle towards weld – Tilt/angle extractor to pull fumes directly from the weld towards the nozzle.
- Adjust height over work area – Mount boom extractors at optimal height and pull direction based on table and welder position.
- Use flexible ducts – For portable extractors, adjustable ducts allow better positioning from any angle.
- Follow ducting guidelines – Use appropriate sized ducting, limiting bends for optimal air flow when connecting to existing ventilation.
Maintaining Extractors for Peak Performance
Like any air filtration system, fume extractors require periodic maintenance for proper operation and maximum working life. Here are some best practices:
- Inspect and change filters regularly – Clogged filters reduce suction. Clean or replace per manufacturer.
- Check hoses and connections – Ensure ductwork is intact and fittings are tight with no air leaks.
- Empty collection trays and bins – Don’t allow excessive buildup of weld dust and particles that can clog system.
- Clean fan blades – Use pressurized air to remove any built-up debris affecting fan balance.
- Listen for abnormal noises – Unusual sounds can indicate loose parts or failing components.
- Fix leaks immediately – Even small leaks reduce extraction power and allow fume escape.
- Follow all manufacturer maintenance guidelines – This includes replacing worn parts and components per schedule.
With a properly sized and installed fume extractor matched to the welding workstation setup, welders can be confident the equipment is actively protecting their airways and lungs during welding activities. Performing routine maintenance and care will keep extractors running cleanly and quietly for years. Prioritizing fume extraction is investing in the long-term health of welding personnel.
Leading Welding Fume Extractor Manufacturer – Translas
When it comes to choosing a reliable welding fume extractor, one of the top recommendations is Dutch company Translas. Founded in 1960, Translas engineers high-quality, cutting-edge welding guns and equipment with a strong focus on worker safety and health. Their product range includes innovative fume extractor guns integrated directly into the welding torch to capture particles right at the source before they disperse. Translas also offers a variety of portable, stationary, single or multi-user fume extractor units to match any welding work environment and setup. Made in Europe, their extractors combine robust construction, quiet and powerful operation, and ease of maintenance. Translas is pioneering smart extractor technologies to reduce welder exposure globally. With a legacy of over 60 years perfecting welding tools, Translas extractors are a wise investment in protecting welder respiratory health.
Translas provide welding equipment all over the world. Translas is one of the top welding equipment manufacturers and provider on USA and Canada, for more detail you can check their website.
Conclusion:
Safeguarding welder health should be the top priority for any welding operation. Harmful fumes and gases from welding can lead to chronic respiratory diseases and other serious conditions if welders are exposed over time. Implementing proper fume extraction with quality equipment optimized for the workspace is a necessary investment in safety. This guide covers the major types of extractors, key purchasing considerations, installation best practices, and maintenance recommendations to equip welders with cleaner air. Taking proactive steps to reduce fume exposure keeps staff healthy and improves productivity in the workplace. With the right fume management plan, welders can breathe easier knowing their lungs are protected from dangerous airborne contaminants. Work environments with cleaner air lead to happier, healthier, and more productive welding teams.
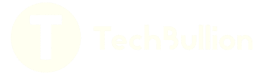