To achieve a successful injection mold design for your project, it is imperative to keep certain factors in mind. Every decision you make, including the materials utilized during production and the effectiveness of your cooling systems, must be meticulously analyzed. This is critical to ensure seamless molding processes and the desired outcomes. This blog post will provide you with three essential tips on injection mold design to help you succeed in creating plastic parts or products.
In this article, we’ll discuss what considerations must be taken when designing the tool cavity’s shape and examining proper ejection system placements. Furthermore, we will provide pertinent information on the right gate location choice and material selection for efficiently manufacturing plastic components. Read on for details!
The Significance of Injection Mold Design
The significance of injection mold design in manufacturing and product development is immense. A well-designed mold ensures superior product quality, precision, and consistency, reducing the risk of defects and improving customer satisfaction. It optimizes production efficiency by considering factors like cycle time and material flow, leading to cost savings and increased output. A durable mold minimizes maintenance costs and ensures uninterrupted production, enhancing long-term sustainability and profitability. Moreover, injection mold design fosters innovation, enabling the creation of complex shapes and designs that captivate consumers and drive market success. In essence, injection mold design shapes the manufacturing landscape, turning dreams into tangible realities that leave a lasting impact on industries and consumers alike.
Benefits of a Good Injection Mold Design
A reliable and responsible manufacturer of injection mold designs can elevate your business to new heights. Let’s explore the advantages they offer:
Cost and Time Savings:
Efficient mold designs optimize material usage, reducing waste and resulting in cost savings. Additionally, well-structured arrangements significantly decrease production time, leading to faster turnaround and increased productivity.
Customer Loyalty:
High-quality products produced from well-designed molds impress customers, fostering trust and loyalty. Consistent product quality builds a strong brand reputation and encourages repeat business.
Quality Assurance:
Well-engineered mold designs ensure that final products consistently meet desired specifications. Minimizing defects and flaws contributes to higher quality end-products, reducing the need for rework and repairs.
Considerations for a Good Injection Mold Design
Several crucial factors must be considered when creating a successful injection mold design. Here are three key considerations:
Materials Selection:
Choosing suitable materials is essential for mold design. It is important to select materials that are durable, heat-resistant, and compatible with the type of plastic used for injection molding. The materials chosen directly impact the performance and longevity of the mold.
Manufacturing Efficiency:
An effective mold design aims to streamline the manufacturing process. It should facilitate easy and smooth material flow during injection, minimizing defects and improving overall productivity.
Corrosion Resistance:
Corrosion can be a significant issue in injection molds, mainly when working with corrosive materials or additives. Designing the mold with corrosion-resistant materials or applying protective coatings can prolong its lifespan and ensure consistent performance.
Introducing JOBR’s Injection Molding Service
Your injection molding needs are in good hands when you partner with JOBR. Whether you’re looking for accuracy or scalability, our specialized manufacturing capabilities always deliver reliable and expert service! And that includes:
Material Variety:
We supply a diverse raw material selection that ranges from rigid plastics to flexible materials, including PEEK, PPSU, PBT, LCP, PBT, etc. Whatever the project requirements, JOBR has you covered.
High Production Volume:
Our advanced mold facility, equipped with state-of-the-art technology and expert craftsmanship, goes above and beyond in delivering top-notch injection molds, enabling us to fulfill high-volume production orders with unparalleled speed and cost-effectiveness.
Lightweight and Corrosion-Resistant:
Our injection molds are lightweight yet sturdy enough for heavy use while highly corrosion-resistant to ensure peace of mind and longevity.
Perfect Surface Finishes:
JOBR offers a wide range of polishes and textures for endowing different features to your parts, allowing you to customize the surface appearance and tactile feel of your products to perfectly align with your customer preferences.
Conclusion:
To sum up, successful injection mold design is characterized by its ability to produce top-notch parts while saving time and costs. A well-engineered mold ensures efficient manufacturing and guarantees customer satisfaction and loyalty. By carefully considering materials, manufacturing efficiency, and corrosion resistance, you can create an optimized mold for custom injection molding.
We at JOBR, with our wide range of materials, high production volume, lightweight and corrosion-resistant molds, and impeccable surface finishes, are a trusted partner for injection molding services. Our expertise and dedication make us the go-to choice for businesses seeking to enhance production capabilities and product quality, such as ABAX, Airthings, and Blueye. So don’t hesitate to contact us to get perfect injection molds!
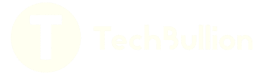