MIM is the introduction of modern plastic injection molding technology into the field of powder metallurgy and the formation of a new metal parts near-net molding processing technology, is in recent years the discipline of powder metallurgy and the industrial field of the rapid development of a high and new technology. MIM process steps are: first of all, selected to meet the requirements of the MIM of the metal powder and the organic binder at a certain temperature under the conditions of the appropriate method of mixing into a homogeneous Feed, and then after granulation in the heated state of plasticization injection molding machine into the mold cavity to obtain forming blanks, and then after chemical or solvent extraction method of degreasing treatment, and finally by the sintering densification to get the final product.
Compared with traditional technology, Metal powder injection molding technology has the following characteristics: high precision, uniform organization, excellent performance, low production costs etc. Its products are widely used in electronic information engineering, medical equipment, office equipment, automobiles, machinery, sports equipment, watches and clocks, weapons and aerospace and other industrial fields.
Metal powder injection molding MIM process using micron-grade fine powder, can accelerate the sintering shrinkage, help to improve the mechanical properties of materials to extend the fatigue life of materials, but also to improve resistance to stress corrosion and magnetic properties. The world’s powder injection molding industry is still small, but which in the economic crisis has not been much affected, but steadily increased. In Europe, its main application area is automotive; in North America, is in medical field; while in Asia in communication products.
Nowadays, China in the consumption of iron powder and copper powder has more than Japan, ranking first in Asia. The future application of powder metallurgy parts are still in the automotive field. From a technical point of view, high-density powder metallurgy parts, new powder metallurgy materials and high-precision powder metallurgy equipment are the future trend of powder metallurgy industry.
The future development of MIM mainly focus on the material and design, using the advantages of this process to help customers improve product design and reduce costs, thereby expanding the application of powder injection molding.
Powder Metallurgy Promote The Development of Spare Parts
In recent years, the rapid economic progress led to the development of some parts manufacturers. Powder metallurgy is a technology which forms material and parts in one, not only energy efficient but also less pollution, saving material, is the most advanced modern technology of manufacturing. Powder metallurgy, in the parts manufacturing industry, has an irreplaceable position and role, which has become the forefront of the parts production.
Thus, it has high requirement on powder metallurgy materials production. In the metallurgical methods, because the powder metallurgy has the preparation process, the composition of the unique advantages of composition, it can produce good materials that in special applications, playing important roles, and has a broad application prospects. Powder metallurgy products are generally used in the manufacture of high-strength wear-resistant parts, machinery, electrical appliances, medical equipment, automotive parts, electrical mechanical, agricultural machinery, motors etc..
Powder metallurgy is an important part forming technology. Industries which use powder metallurgy technology will not only promote the advanced development of the industry, but also bring a bright way for future spare parts production.
Powder Metallurgy Can Solve The Forming Problem of Ti-Al Alloy
In recent years, in order to promote the high temperature and high performance niobium titanium aluminum alloy technology engineering and industrialization process,a China-made of independent intellectual property rights, new generation aerospace engine material—-high temperature and high performance niobium-titanium-aluminum alloy material, will be in process of mass production, which enable China’s aerospace engine materials in the world leading level. High-niobium titanium aluminum alloy is China’s innovative research direction, with the world’s first high-temperature alloy patents, led the world in the field of research and development in the development of titanium alloy landmark, marking China’s titanium aluminum inter-metallic compounds research areas in an international leader. China has put titanium aluminum alloy research in the national 863 high-tech new materials development plan. After years of efforts, in the aspects of alloy micro-structure, deformation characteristics, the impact of additional elements and alloy preparation technology, China has achieved lots of fruitful work, also had a number of articles published on titanium aluminum alloy in domestic and foreign journals and academic conference.
Titanium aluminum alloy processing technology is: (1) ingot metallurgical technology; (2) powder metallurgy technology; (3) rapid condensation technology; (4) composite materials technology. Ti-Al alloy ingot metallurgy technology has some problems such as segregation and inhomogeneity of the ingot composition. The Ti-Al alloy powder produced by rapid condensation technology has stable chemical composition and good process performance. However, with the change of heat treatment temperature, the micro-structure And the micro-hardness will change accordingly. The titanium-aluminum alloy made by the composite technology shows good strengthening performance, but the problems such as the transverse performance and environmental resistance are still need to be solved; Powder metallurgy method can produce uniform and small parts, The near-net shape of the workpiece can be realized, which can effectively solve the problem that the Ti-Al intermetallic alloy is difficult to be formed. At present, there are two main methods of powder milling: elemental powder and titanium alloy pre-alloy powder. Domestic scholars prefer to use elemental powder technology to make titanium aluminum alloy.
Harber Metal Ltd. is a powder metallurgy manufacturing company created since 2014, with good production facilities and advanced technology, and is now into the production of iron-based powder metallurgy and stainless steel powder metallurgy. The company covers an area of 5,000 square meters, with 1,600 square meters of workshop, and dozens of sets of automatic presses from 100 tons to 5 tons for powder metallurgy. There are dozens of sets of automatic presses for powder metallurgy ranging from 100 tons to 5 tons, as well as complete product testing equipment and matching powder metallurgy mold processing equipment. Now the company has an annual output of 500 tons, about 5 million pieces of powder metallurgy products. products per year.
https://www.harbermetal.com/
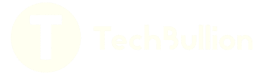