Stepping into the future of sustainable energy, the spotlight is turning towards dimethyl ether (DME), also known as methoxymethane, a compound proving invaluable for both green fuel and downstream petrochemical industries. This discussion takes us through a detailed understanding of DME, from its elementary properties to its potential as a sustainable energy source.
Unveiling the Characteristics of DME
DME, represented chemically as CH3-O-CH3, holds the distinction of being the simplest Aliphatic ether, a fact first recorded by esteemed chemist Alexander Williamson. Upon ignition, DME combusts into a unique blue flame and doesn’t require an external indicator like methane due to its characteristic sweet, ether-like smell. At a structural level, it is composed of two methyl groups bonded to an oxygen atom and is predominantly derived from methanol (CH3OH), by replacing a hydrogen atom with a methyl group. It has a normal boiling point of -25 degrees Celsius and, due to its high saturated vapor pressure at ambient temperature (1.6 atmospheres), it liquefies effortlessly under a pressure of 5-6 bars. The ease with which it transitions from gas to liquid, coupled with its high thermal energy content, earmarks DME as an exciting emerging source of energy.
The Eco-friendly Nature and Diverse Applications of DME
Among DME’s many attributes, its eco-compatibility stands out. It can be found in daily use items like spray canisters designed for direct human contact. DME has a short lifespan in the atmosphere (half-life of one day), thoroughly disintegrates in the troposphere, and, importantly, poses no threat to the ozone layer. Its chemical stability, non-corrosive nature, non-carcinogenic properties, near non-toxicity, and the fact that it doesn’t form organic peroxides even after long-term exposure to air further underscore its environmental credentials.
When it comes to purity and cetane index, DME significantly outperforms traditional fuels like methane, methanol, propane, and diesel. Its high solubility coefficient enables it to function as a solvent in aerosol formulation, a property particularly useful when dealing with low-solubility components. Additionally, the harmful effects of CFC compounds on the ozone layer have propelled DME into the spotlight as an effective substitute, leading to its adoption in refrigeration cycles. Recent advancements have even proposed its use in fuel cells and the manufacturing of light olefins.
On an industrial scale, DME serves as a handy precursor for synthesizing other organic compounds. For instance, dimethyl sulfate can be produced by combining dimethyl ether and sulfur trioxide, while the Monsanto process leverages DME for acetic acid production. With its low boiling point, DME is also an efficient extraction agent and solvent in labs as it can easily be separated from reaction mixtures. Moreover, a combination of dimethyl ether and propane is employed in treating warts.
However, the uses of DME aren’t confined to industrial and medical fields. It finds application in everyday products like hair sprays, glues, and as a blowing agent in polymer foams and insulators. DME is also used alongside ammonia, carbon dioxide, butane, and propane in microwaves and as a humectant. Its negligible soot emission and non-toxicity make it an attractive substitute for propane, methanol, diesel, and gasoline in liquid fuels. The use of DME extends to power plant fuels, cell fuels, vehicle fuels, and the generation of electricity, as well as for heating and cooking purposes.
The Process of DME Production
DME can be produced using two distinct methods, both of which use methane-containing raw materials such as natural gas, coal, oil, biomass, among others. The first, and currently the most popular, is the indirect synthesis of DME. In this method, the raw material is initially converted into synthesis gas, a blend of hydrogen and carbon monoxide. This gas then transforms into methanol via a catalyst and is subsequently dehydrated in the presence of another catalyst to yield DME. This two-step procedure, involving methanol production followed by DME synthesis, categorizes this method as indirect.
The second method, known as direct synthesis, eliminates the need for methanol production, allowing DME to be produced directly from synthesis gas. This single-step process enhances the speed of synthesis gas to DME conversion and decreases production costs due to the reactor’s simpler design.
Looking Back at DME Research
Industrial DME production typically relies on methanol dehydration in an adiabatic flow reactor. Considerable research has focused on simulating these reactors’ behaviour, but it wasn’t until 1996 that a comprehensive solution was put forth using the Newton-Raphson method to solve nonlinear partial differential equations for flow reactors with axial mixing in isothermal and adiabatic states. Subsequent studies have further deepened our knowledge of adiabatic flow reactors and DME production.
Investing in the Future with DME
Considering the current global market trends, the steady economic growth of DME over the last decade, and the considerable potential of this product, it is clear that DME presents a highly attractive investment opportunity. Establishing a petrochemical plant capable of producing a million tons per year would require an estimated investment of around 600 million euros. Such an investment can yield up to 60% IR with a payback period of 2 to 3 years.
It’s worth mentioning that our engineering group has performed simulations of the plant operation using various production methods, including production from natural gas, methanol, coal, and waste. Given that only a handful of companies currently possess the technology to manufacture DME, coupled with a robust global market capacity, this makes for a profitable venture.
With a decade’s worth of experience in managing upstream petrochemical projects, I, Ali Dabiran, am eager to collaborate with potential investors. The future of DME as a clean fuel source cannot be overstated. Furthermore, the role of DME as a catalyst in downstream petrochemical industries, such as propylene, light and heavy polyethylene, polyester resin, rubber plants, and refrigeration plants, has the potential to significantly reduce fixed investment. It’s clear that DME is more than just a sustainable fuel source; it’s a strategic component in the global energy landscape.
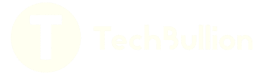