Bearing tolerance plays a crucial role in the performance and reliability of industrial machinery. As an industrialist or manufacturer in the bearing industry, it is essential to have a comprehensive understanding of bearing tolerance and its significance. In this in-depth guide, we will explore the concept of bearing tolerance, its types, factors affecting it, benefits, tolerance grades, proper selection, common challenges, and real-world examples.
By delving into this topic, you will be equipped with the knowledge to optimize bearing tolerance in your applications, leading to improved performance and efficiency.
What is Bearing Tolerance?
Bearing tolerance refers to the allowable deviation in the dimensions and operating characteristics of a bearing. It determines the range of permissible variation to ensure proper fit, clearance, and preload, enabling bearings to function optimally. Manufacturers carefully control tolerance during the production process to achieve consistent performance and meet specific application requirements.
Types of Bearing Tolerance
Radial Bearing Tolerance: Radial bearing tolerance focuses on the clearance and preload of the bearing. Clearance refers to the space between the bearing’s rolling elements and the inner and outer races. It ensures smooth operation and minimizes the risk of excessive friction and heat generation.
Preload, on the other hand, is the intentional application of a load to the bearing to ensure proper contact between the rolling elements and races. Preload eliminates clearance, minimizing axial and radial play.
Axial Bearing Tolerance: Axial bearing tolerance is concerned with the axial clearance and axial preload. Axial clearance refers to the amount of axial movement permitted between the bearing’s races and rolling elements. Proper axial clearance prevents excessive axial play, ensuring stability and load distribution.
Axial preload, on the other hand, involves applying an axial force to remove axial clearance. Axial preload enhances stiffness and minimizes axial deflection, which is beneficial in applications with variable loads or high precision requirements.
Factors Affecting Bearing Tolerance
Several factors influence bearing tolerance and should be taken into consideration:
Manufacturing Processes: Precision machining techniques and quality control measures employed during bearing production determine the achievable tolerance levels. Factors such as material selection, heat treatment, and surface finishing impact the final tolerance of the bearing.
Material Selection: The properties of bearing materials, such as steel alloys, impact the tolerance of the bearing. Proper material selection is vital to ensure dimensional stability, resistance to wear, and fatigue strength.
Environmental Conditions: Environmental factors such as temperature variations, humidity, and exposure to contaminants can affect bearing dimensions, clearance, and preload. Bearing designs should consider these factors to ensure optimal performance and longevity.
Operating Conditions: Load, speed, and lubrication conditions play a crucial role in bearing performance and tolerance requirements. Understanding the specific application’s demands is essential for selecting the appropriate tolerance.
Benefits of Proper Bearing Tolerance
Maintaining proper bearing tolerance offers several advantages for industrialists and manufacturers:
Improved Performance and Efficiency: Optimal bearing tolerance ensures proper load distribution, reducing friction, heat generation, and energy losses. This leads to improved machine performance, increased efficiency, and reduced operating costs.
Extended Service Life: Bearings with the correct tolerance experience less wear and fatigue, resulting in longer service intervals and reduced downtime. This translates to cost savings and increased productivity.
Reduced Vibration and Noise: Bearings with good tolerance minimize vibration, leading to smoother operation and quieter machinery. This improves operator comfort and reduces the risk of damage caused by excessive vibration.
Enhanced Reliability and Safety: Accurate tolerance selection enhances bearing reliability, reducing the likelihood of premature failures and associated safety risks. This is particularly important in critical applications where downtime or failure can have severe consequences.
Bearing Tolerance Grades: Bearing tolerance is defined by international standards, including ISO (International Organization for Standardization) and ANSI/ABMA (American National Standards Institute/American Bearing Manufacturers Association). These standards classify tolerance into different grades, indicating the level of precision and control in bearing manufacturing. Common tolerance grades include P0, P6, P5, and P4. Each grade has specific criteria for dimensional accuracy and running accuracy.
Proper Selection and Application of Bearings with the Right Tolerance
Selecting bearings with the appropriate tolerance requires careful consideration of various factors:
Application Requirements: Evaluate the load, speed, and operating conditions to determine the required tolerance grade. Heavy-duty applications may require higher precision bearings than standard applications.
Compatibility: Ensure the selected bearing tolerance aligns with other components in the system, including shaft and housing fits. Proper fit and alignment are crucial for optimal performance and longevity.
Expert Guidance and Technical Support: Consult with bearing specialists and experts to gain valuable insights and recommendations. They can provide guidance on bearing selection, application-specific requirements, and optimal tolerance levels based on their industry knowledge and experience.
Common Challenges and Solutions in Bearing Tolerance: Industrialists and manufacturers may encounter challenges related to bearing tolerance. Here are some common issues and their solutions:
Tolerance Stack-up: When multiple components are assembled, the cumulative effect of their tolerances can result in undesirable variations. Proper engineering and design practices, along with careful tolerance analysis, can help mitigate this challenge.
Temperature and Lubrication Challenges: High temperatures and inadequate lubrication can affect bearing dimensions and cause changes in tolerance. Selecting bearings with appropriate heat resistance and using proper lubrication can address these challenges.
Dynamic Loads and Variations: Dynamic loads and variations in operating conditions can impact bearing tolerance. By accurately assessing the application requirements and selecting bearings with suitable tolerance, these challenges can be overcome.
Real-world examples highlight the significance of bearing tolerance optimization. Here is a small excerpt:
In a heavy-duty manufacturing facility, upgrading to bearings with tighter tolerance resulted in reduced vibration, improved machine performance, and extended service life.
A steel mill implemented precision bearings with the correct tolerance for their rolling mill applications, leading to enhanced reliability, increased productivity, and cost savings due to minimized downtime.
Conclusion
Understanding bearing tolerance is crucial for industrialists and manufacturers in the bearing industry. Proper tolerance selection based on factors such as load, speed, and operating conditions leads to improved performance, extended service life, and enhanced reliability. With their expertise in bearing solutions, KG International Group is well-equipped to provide guidance and support in optimizing bearing tolerance for your specific applications. Embrace the power of bearing tolerance and unlock the full potential of your machinery’s performance and efficiency.
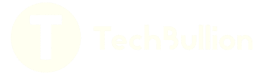