Introduction
In the fast-paced world of product development, staying ahead of the competition requires innovative and efficient design processes. The advent of 3D modeling technology has revolutionized the way products are designed, allowing for greater precision, flexibility, and cost-effectiveness. This blog will delve into the realm of 3D modeling and explore its significant role in product development, highlighting its benefits, tools, and best practices.
Understanding 3D Modeling
3D modeling is the process of creating a three-dimensional digital representation of an object using specialized software. It enables designers and engineers to visualize and manipulate objects from various angles, helping them better understand their form, dimensions, and functionality. By constructing virtual prototypes, product developers can iterate and refine their designs before physically producing them.
Benefits of 3D Modeling in Product Development
2.1. Enhanced Visualization and Communication
3D models provide a realistic representation of a product, allowing designers to visualize and share their ideas more effectively. Stakeholders can better understand the design intent, reducing the chances of miscommunication and facilitating informed decision-making throughout the development process.
2.2. Iterative Design Process
With 3D modeling, designers can easily make changes and iterations to their prototypes without incurring significant costs or time delays. This iterative process enables faster design improvements, leading to higher-quality end products and minimizing the risk of costly design flaws.
2.3. Precise Measurements and Analysis
3D modeling tools offer accurate measurements and analysis capabilities, ensuring that product dimensions, tolerances, and functionality are meticulously considered. This helps identify potential issues early in the design stage and avoid costly manufacturing errors.
2.4. Cost and Time Efficiency
By eliminating the need for physical prototypes in the early stages of product development, 3D modeling significantly reduces costs associated with materials, labor, and machining. It also shortens the time-to-market, as designs can be shared and evaluated quickly, accelerating the overall development process.
Key 3D Modeling Tools
3.1. Computer-Aided Design (CAD) Software
CAD software, such as SolidWorks, AutoCAD, or Fusion 360, provides a comprehensive set of tools for creating precise and detailed 3D models. These tools allow designers to manipulate geometries, apply textures and materials, simulate real-world physics, and perform complex simulations and analysis.
3.2. Sculpting Software
Sculpting software, like ZBrush or Blender, is ideal for creating organic shapes and intricate details. It enables designers to sculpt virtual models using digital brushes and intuitive sculpting tools, providing a more artistic approach to 3D modeling.
3.3. Parametric Modeling
Parametric modeling software, such as Siemens NX or PTC Creo, allows designers to create 3D models based on parameters and constraints. This approach facilitates quick modifications and updates to designs by adjusting the input parameters, automatically updating the entire model accordingly.
Best Practices for Effective 3D Modeling
4.1. Plan and Sketch
Before diving into 3D modeling, it is crucial to have a well-defined plan and sketch of your design. This helps establish a clear direction and reduces the likelihood of getting sidetracked during the modeling process.
4.2. Maintain Design Intent
Throughout the modeling process, ensure that your design intent is consistently upheld. This means considering factors such as manufacturability, assembly, and maintenance requirements to ensure the end product is functional and practical.
Additional Information and Best Practices
5.1. Collaborative Design
3D modeling facilitates collaboration among multidisciplinary teams by allowing simultaneous access and real-time updates to the design files.
Use cloud-based platforms or version control systems to manage and track design revisions, ensuring everyone is working with the latest version.
5.2. Consider Manufacturing Constraints
Keep in mind the manufacturing processes and constraints while designing your product. Consider factors like material selection, tooling requirements, and assembly methods to optimize the manufacturing process.
5.3. Validate Designs with Simulation
Take advantage of simulation tools within your 3D modeling software to evaluate the performance and behavior of your product in different scenarios.
Perform structural, thermal, or fluid dynamics analysis to ensure the design meets the required specifications and standards.
5.4. Embrace 3D Printing for Rapid Prototyping
3D modeling seamlessly integrates with 3D printing technology, enabling rapid prototyping and the production of physical models for testing and validation.
Use 3D printing to verify the fit, form, and function of your design before committing to costly manufacturing processes.
5.5. Test for Ergonomics and User Experience
Utilize 3D modeling to assess the ergonomics and user experience of your product.
Create virtual mock-ups and conduct virtual user tests to evaluate how users interact with the product and make necessary adjustments to improve usability.
5.6. Document and Organize Design Files
Maintain a well-structured file management system to store and organize your design files, ensuring easy retrieval and future reference.
Include proper annotations, labels, and documentation within the 3D models to provide comprehensive information to stakeholders.
Advanced Techniques in 3D Modeling
6.1. Parametric Design
Parametric design involves using mathematical relationships and constraints to drive the shape and behavior of the 3D model.
By defining parameters and variables, designers can create models that adapt and update automatically when changes are made, making it easier to explore different design options.
6.2. Generative Design
Generative design employs algorithms and computational methods to generate optimized designs based on specified criteria and constraints.
By inputting design goals and performance parameters, designers can explore numerous design variations and discover innovative solutions that may not have been considered otherwise.
Integration with Virtual Reality (VR) and Augmented Reality (AR)
7.1. Virtual Reality (VR)
Virtual reality allows designers to immerse themselves in a virtual environment and interact with their 3D models at a human-scale.
Designers can visualize their creations in a realistic context, gaining insights into ergonomics, aesthetics, and overall user experience.
7.2. Augmented Reality (AR)
Augmented reality enables designers to overlay virtual 3D models onto the physical world, creating a blended reality experience.
Designers can visualize how the product will look and behave in real-world settings, facilitating design validation and collaboration.
Industry Applications of 3D Modeling in Product Development
8.1. Automotive Industry
3D modeling plays a vital role in designing vehicle components, optimizing aerodynamics, and simulating crash tests.
It enables automotive manufacturers to streamline the design process, improve fuel efficiency, and enhance safety features.
8.2. Consumer Electronics
In the consumer electronics sector, 3D modeling is used to create sleek and ergonomic product designs, ensuring proper component placement and efficient thermal management.
It allows for the visualization of user interfaces and interactions, leading to intuitive and user-friendly products.
8.3. Architecture and Construction
Architects and construction professionals utilize 3D modeling to design and visualize buildings, enabling accurate representation of spatial relationships and materials.
It aids in identifying clashes, optimizing layouts, and presenting realistic renderings to clients.
Future Trends in 3D Modeling for Product Development
9.1. Integration of Artificial Intelligence (AI)
AI-powered algorithms can enhance the design process by automating repetitive tasks, generating design variations, and predicting product performance.
Machine learning algorithms can analyze vast amounts of data to identify patterns and optimize designs based on user preferences and feedback.
9.2. Cloud Collaboration and Storage
Cloud-based 3D modeling platforms and storage solutions enable real-time collaboration among distributed teams.
Designers can work simultaneously, share updates instantly, and access their files from anywhere, improving efficiency and reducing the limitations of physical infrastructure.
Challenges and Considerations in 3D Modeling
10.1. Learning Curve
Mastering 3D modeling software requires time and effort. It involves understanding complex interfaces, tools, and techniques.
Designers and engineers may need to invest in training programs or seek assistance from experienced professionals to overcome the initial learning curve.
10.2. Hardware Requirements
Many 3D modeling software as cited by Myarticles can be resource-intensive, requiring powerful hardware to ensure smooth operation and efficient rendering.
Designers may need to invest in high-performance computers or workstations with robust graphics cards and ample storage capacity.
10.3. File Compatibility and Interoperability
Collaborating with stakeholders who use different 3D modeling software can present challenges in terms of file compatibility and interoperability.
Designers should consider using industry-standard file formats or tools that allow for seamless import and export of files across different software platforms.
Ethical Considerations in 3D Modeling
11.1. Intellectual Property and Copyright
When using 3D models, designers must respect intellectual property rights and avoid infringing on copyrighted designs.
It is important to create original designs or obtain proper licensing or permissions when using existing designs or components.
11.2. Design Bias and Representation
Designers should be mindful of design biases that can perpetuate stereotypes or exclude certain user groups.
Ensuring diversity and inclusivity in the design process helps create products that cater to a wide range of users and address their unique needs.
The Future of 3D Modeling in Product Development
12.1. Real-Time Collaboration and Co-Creation
Advancements in network technologies and cloud-based platforms will enable real-time collaboration and co-creation among designers, engineers, and stakeholders from different locations.
This will enhance communication, streamline decision-making, and foster innovation by leveraging collective expertise.
12.2. Simulation and Optimization
The integration of 3D modeling with advanced simulation tools will allow for real-time performance evaluation and optimization during the design process.
Designers can iterate designs quickly, making data-driven decisions that result in highly efficient and optimized products.
12.3. Additive Manufacturing and Customization
3D modeling is closely tied to additive manufacturing (3D printing), enabling the production of customized products on-demand.
The combination of 3D modeling and additive manufacturing opens up new possibilities for mass customization, reducing waste and increasing customer satisfaction.
Cost Considerations in 3D Modeling
13.1. Software Licensing
Depending on the complexity and features required, 3D modeling software licenses can vary significantly in cost.
Consider the needs of your project and budget constraints when selecting the appropriate software.
13.2. Hardware Investment
Alongside software costs, it’s important to factor in the hardware requirements for running 3D modeling software smoothly.
High-performance computers, graphics cards, and storage solutions may require additional investment.
13.3. Training and Skill Development
Training programs or courses may be necessary to acquire the skills needed for proficient 3D modeling.
Consider the cost of training and the time investment required for individuals or teams to become proficient in using the software effectively.
Sustainability and Environmental Impact
14.1. Material Optimization
3D modeling allows for efficient material utilization, minimizing waste during the manufacturing process.
Designers can optimize structures and geometries to reduce the amount of material required without compromising product performance.
14.2. Product Lifecycle Analysis
3D modeling enables designers to conduct lifecycle analysis, evaluating the environmental impact of a product from its creation to disposal.
This analysis helps identify opportunities for improvement, such as reducing energy consumption, selecting recyclable materials, or designing for disassembly.
Emerging Technologies and 3D Modeling
15.1. Artificial Intelligence and Machine Learning
AI and machine learning algorithms can be integrated into 3D modeling software to automate tasks, optimize designs, and enhance productivity.
These technologies can assist in generating design variations, predicting performance outcomes, and reducing manual effort.
15.2. Virtual Reality (VR) and Augmented Reality (AR) Enhancements
VR and AR technologies continue to advance, enhancing the immersive and interactive aspects of 3D modeling.
Designers can expect more realistic virtual environments, improved collaboration features, and enhanced user experiences.
Case Studies and Success Stories
16.1. Tesla’s Design and Prototyping Process
Tesla utilizes 3D modeling extensively in the design and prototyping of their electric vehicles, enabling rapid iteration and optimization.
The ability to visualize and simulate designs in 3D has contributed to Tesla’s innovative and industry-leading vehicle designs.
16.2. Nike’s Customization and Personalization
Nike leverages 3D modeling to offer customized and personalized footwear solutions to their customers.
Using advanced 3D scanning and modeling techniques, Nike creates personalized designs that perfectly fit an individual’s unique requirements.
Data Security and Intellectual Property Protection
17.1. Data Backup and Recovery
Implement robust data backup and recovery systems to protect 3D design files from loss or damage.
Regularly backup files to secure storage locations to ensure the availability and integrity of the design data.
17.2. Intellectual Property Protection
Designers should be mindful of protecting their intellectual property rights and confidential designs.
Consider using non-disclosure agreements (NDAs) and other legal measures to safeguard sensitive design information.
Integration with Product Lifecycle Management (PLM) Systems
18.1. Streamlined Design-to-Manufacturing Process
Integrating 3D modeling with PLM systems enables seamless collaboration and data exchange between design and manufacturing teams.
It streamlines the transition from design to production, reducing errors and ensuring a smooth handover of design data.
18.2. Version Control and Design History
PLM systems with version control capabilities help track changes made during the design process and maintain a comprehensive design history.
This allows for better traceability, accountability, and the ability to revert to previous design iterations if needed.
Training and Skill Development
19.1. Continuous Learning and Skill Enhancement
Encourage designers and engineers to continuously update their skills and stay abreast of the latest 3D modeling techniques and software advancements.
Invest in training programs, workshops, and certifications to ensure teams are equipped with the knowledge and expertise needed to maximize the benefits of 3D modeling. 3D Modeling Services provide a freeform pattern on its surface.
19.2. Collaboration and Knowledge Sharing
Foster a culture of collaboration and knowledge sharing within the organization to encourage the exchange of best practices, tips, and tricks among team members.
Establish internal forums or platforms where designers can share their experiences, challenges, and solutions related to 3D modeling.
Industry Standards and Certifications
20.1. Compliance with Industry Standards
Depending on the industry, certain standards and regulations may govern product design and development processes.
Ensure that the 3D modeling practices align with industry-specific standards to meet quality, safety, and regulatory requirements.
20.2. Professional Certifications
Encourage designers and engineers to pursue professional certifications specific to 3D modeling, such as Certified SOLIDWORKS Professional (CSWP) or Autodesk Certified Professional (ACP).
These certifications validate expertise and provide recognition in the industry.
Conclusion
Incorporating additional considerations such as data security, intellectual property protection, PLM integration, training, and industry standards strengthens the overall 3D modeling process in product development. By prioritizing these aspects, organizations can ensure data integrity, streamline collaboration, and enhance the skills of their design teams. With a robust foundation in place, designers and engineers can leverage the full potential of 3D modeling to create innovative and successful products. So, embrace these additional factors, and embark on a journey of efficient and secure 3D modeling in your product development endeavors.
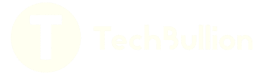