In the world of product development, rapid prototyping has long been a valuable tool for designers and engineers alike. The ability to create a physical prototype allows for a better understanding of a product’s functionality, real-world performance, and aesthetics. But the traditional methods of producing these prototypes have their own set of limitations. Enter 3D printing, a game-changing technology revolutionizing how products are brought to life.
3D printing allows for the creation of three-dimensional objects by successively layering material based on a digital design file. This innovative technology has garnered significant attention in recent years due to its potential to transform industries and disrupt traditional manufacturing processes.
One area which stands to benefit greatly from 3D printing is prototype performance. Innovate your prototyping with MNLs 3D printers today and embrace creativity like never before. Here are eight key ways 3D printers are changing the face of prototype performance:
1. Accelerated Design and Development Process
One of the most notable advantages of 3D printing in prototyping is the remarkable pace designers can move through iterations. Faster production of new designs means shorter development cycles, enabling businesses to bring products to market quickly. This increased speed naturally translates into better sales and improved profits for companies.
2. Realistic Representations
A 3D print allows for accurate replication of the designer’s vision by transforming conceptual sketches into tangible prototypes. These exhibits serve to get an idea across to stakeholders and clients and help identify flaws or improvements that might need attention. Having a physical representation provides a clear understanding of how the final product would look and function, allowing designers to optimize their designs accordingly.
3. Material Diversity
Due to high costs and production lead times, traditional prototyping techniques often restrict material choices. On the other hand, recent developments in 3D printing materials have opened new doors for producing prototypes with specific stress requirements or characteristics that closely match the final product. Advanced materials such as carbon fiber-reinforced composites or metallic alloys allow researchers and engineers to explore innovative engineering solutions that were not feasible before.
4. Reduced Costs
Before 3D printing entered the scene, manufacturers spent large sums on creating molds and specialized tools for each prototype iteration. Today, additive manufacturing technology uses only the necessary material to create prototypes layer by layer, reducing material waste and minimal tooling costs. This cost reduction, coupled with the elimination of time-consuming steps, allows businesses to allocate saved resources to other vital aspects of product development.
5. Customization
The ability to tailor and personalize products is becoming increasingly important across numerous industries. Thanks to the versatility 3D printing offers, designers can effortlessly incorporate custom modifications into their prototypes, addressing unique customer needs or use cases. The technology allows designers to tweak dimensions, alter mechanical properties, or implement design changes easily without having to start from scratch.
6. Enhanced Validation Process
Evaluating a prototype before moving it into mass production is a critical step within the product development life cycle. By leveraging 3D printing technologies, engineers can now thoroughly test and validate individual components or complex assemblies’ functionality and durability under real-life conditions. This robust verification process significantly decreases the risk of expensive design flaws going unnoticed until later production stages.
7. Geographical Flexibility
Traditionally, prototyping services were often limited by geographical barriers due to the necessity of transferring molds or specialized equipment between locations. However, with 3D printing being rapidly adopted worldwide, companies can now develop and share digital design files efficiently across various locations. Instant access to a broad network of connected 3D printers paves the way for decentralized manufacturing that expands collaboration and eliminates logistical constraints.
8. Sustainability
Rapid prototyping methods have been heralded as environmentally friendly alternatives compared to traditional techniques because they considerably reduce waste production. As additive processes involve building objects with only the required materials, excess scrap does not accumulate during parts manufacturing – minimizing the environmental impact.
Undoubtedly, 3D printers have revolutionized the way we create prototypes. Embracing this transformative technology empowers organizations to remain agile in fluctuating markets while fostering a culture of innovation that drives business success.
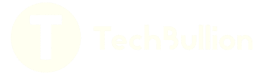