Have you heard of predictive maintenance and how it can benefit you and your organization?
Predictive maintenance is a way to keep your machines working efficiently. It goes into effect before an impending failure happens.
You’ll avoid risking the safety of your employees. It will also avoid the constant interruptions that machine failure brings to your business. Sound good? Read on to learn three things you should know.
What is Predictive Maintenance?
Predictive maintenance forecasts possible system failure before it happens. It detects any early signs of an equipment failure or a misaligned condition of a system.
The idea behind this is to identify any potential issue in advance. Specifically before it escalates into a complete system failure.
Preventive maintenance prevents any asset failure or system dysfunction. This is to ensure that the system is up and running with minimum downtime.
What are the Benefits?
It is an effective way of ensuring assets and infrastructure remain efficient and operational. They provide insights on the condition of assets. They also allow to identify tasks before they cause any significant disruption.
One of the primary benefit is cost savings. It is often more affordable than running repairs after an asset has become inoperable.
Predictive maintenance can diagnose potential problems before they lead to equipment failure. When that happens, the cost of repairs are usually minimized.
This also increases the life cycle of assets and reduces downtime. Last but not least, predictive maintenance allows organizations to develop a proactive approach. This enables the organization to remain proactively prepared for any unforeseen events.
How It is Applied
Predictive maintenance uses a combination of analytical observations, data collection, and mathematical models. Data is collected from sensors. These sensors measure temperature, vibrations, pressure, and other parameters of the equipment.
This predicts when the equipment will require maintenance or repairs. Models predict failures or maintenance needs by observing how the equipment operates and how it has responded in the past.
In some cases, they use artificial intelligence to identify patterns. They also predict potential problems and allows proactive maintenance to carry out.
How To Train For Preventive Maintenance
How to train for preventive maintenance starts with learning how to identify potential problems and how to resolve them. Employees need to have an understanding of the fundamentals of predictive maintenance. This includes machine learning and predictive analytics.
Organizations should also invest in technology that can monitor machines and other equipment. They should invest on in technology that provide more accurate and earlier notification of problems. Through this training, organizations are not only prepared for potential issues. They are also efficient on the resources needed for maintenance.
If you want to train on predictive maintenance, check this SFMECA training linked here.
Explore More About Predictive Maintenance
Predictive maintenance can help companies save money, reduce downtime and increase safety. Companies should ensure they partner with a qualified service provider to make sure that it is implemented correctly.
Businesses should strongly consider investing in predictive maintenance to maximize operational efficiency.
Check out our blog for more informative reads like this one!
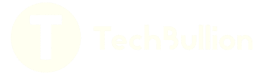