Abdallah Salloum is a talented mind with a rich resume in transforming business processes to impact organization-wide results. His professional journey began as a line worker for Mazda motor manufacturing while he completed his undergraduate and graduate degrees. As he grew professionally, his business systems and project management acumen led to greater responsibility and a number of leadership roles in industrial manufacturing. Mr. Salloum began working for GE Healthcare in 2017, where he led the initiative to drive the flagship MRI supply chain division to $2.5 billion in revenue.
What is a typical day like in the life of a Manufacturing Engineer?
This depends on the manufacturing engineer’s immediate area of focus. If he’s in AMET, he’s either spending his time in a pilot factory conducting experiments or monitoring techs like robotics, machining, welding, or injection molding. This engineer is monitoring tech performance in the spirit of determining whether it should be included in the overall AME portfolio or if it should ultimately be rejected.
Manufacturing engineers continue to optimize tech, they attend conferences, speaking with teams that are developing the tech. While the AMET team is not directly developing the tech, they’re leveraging their industry expertise to ensure advanced manufacturing tech is brought in-house with the purpose of positively affecting new product introduction (NPI) or introduced to enhance existing manufacturing efficiency.
How does an Industrial Project Manager spend a typical day?
An Industrial Project Manager’s Day is extremely involved, particularly as it has to do with the NPIs. On any given day, the IPM is balancing three to four medium-sized projects as well as two to four large new product introductions—all at different phases of the pipeline. With every project, it’s important to verify and understand whether the design for manufacturability, serviceability, assembly, and reliability was vetted and the outcome is understood and mitigated. Industrial Project Managers must consistently ask, “does the product, as it’s introduced to manufacturing, bring value to the business case that was initially considered when the decision was made to introduce the product?”
A program managing team is involved in putting together a full industrial solution for the manufacturing plant, and a continuous dialogue must be present between project engineering and manufacturing engineering. That’s what ensures synchronicity. The Industrial Project Manager becomes the Maestro for the new product introduction, as it pertains to the industrialization of the product or project.
How does the day breakdown for the team working on Standards & Process?
The folks who spend their time on the Standards & Process team split their time between continually monitoring and analyzing existing processes and engaging those processes that live in the manufacturing facility, helping to understand where the plant is running into problems. These functions help determine how the team can help support and enable success with new tools or process changes to improve Safety, Quality, Delivery, and Cost.
What made you interested in the field of manufacturing engineering?
While I am not a manufacturing engineer, nor have I had a formal engineering education, at heart and by trade, I support advanced engineering practice and believe it is the backbone of any industrial manufacturing organization. Many organizations do not understand and underestimate the impact of the industrialization phase as part of the product life cycle, and then struggle immensely when the product is launched. When industrialization is poorly executed or missing and a product is lobbed over the fence to manufacturing, the project fails before it has a chance to perform and becomes a margin drain not to mention a negative customer experience.
When manufacturing remains uninvolved in the design ensuring design-for-X (serviceability, assembly, etc…) and implementing relevant tech early on, they cannot ensure an efficient, effective, new product introduction. When the importance of each phase of the product life cycle goes unrecognized or is not acknowledged, the process becomes more about check-the-box than operational, and teams struggle to launch products successfully – customers become disappointed, and time and money are wasted which could have been saved in a properly executed new product introduction cycle. I came to this realization after having been involved in fixing too many product/process launches and conducting several “post-mortem” analyses to understand root-cause.
A well-executed new product introduction is enormously effective – when I was leading a $3.5B automotive TIERI supplier in Europe and by placing the right emphasis on industrialization, the team was able not just to launch successfully but to also reduce overall manufacturing cost by 3.5% of sales translating into $120M bottom line impact. These stunning results are within grasp and proof that proper industrialization effort and investment are very rewarding.
Key Takeaways
Advanced Manufacturing Engineers work with products that have varying degrees of intricacy in the design and project scope.
The way a manufacturing engineer spends his day is determined by the scope of his work.
AME teams leverage industry expertise in order to bring new tech and process in-house as a mechanism for improving current processes and addressing manufacturing needs.
There are specific components to a product life cycle and successfully launching a product comes down to mastering each of these phases and working synergistically to meet a common goal.
To learn more about Abdallah Salloum, please visit his Crunchbase profile.
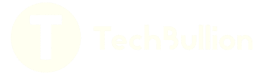