There are two types of metal casting services: investment casting and sand casting service, which both involve pouring liquid metal into a mold and creating a metal part. As each has its own advantages, you can’t simply say which one is better, but rather which one will be more appropriate for your product.
In investment casting, the metal is formed using a lost wax process that uses aluminum molds, but steel molds are useful if the component quantity is large. The first step is to make a set of molds, the lost wax casting molds are typically made of aluminum, but steel molds can also be used for larger components. As part of investment casting, also known as a lost wax casting, wax is injected into the mold in order to create a wax pattern. Once the wax pattern has been assembled onto a sprue (or tree), it is then coated with refractory slurry and wrapped around the outside of the tree to make a ceramic shell. The molten metal is poured into the shell. Once it cools, it becomes metal casting. Investment casting has the following benefits:
- High dimensional accuracy can be achieved with investment castings.
- The investment casting process is capable of producing parts with complex shapes and very thin walls.
- Investment casting can use ferrous, nonferrous, or duplex alloys as the material. Repeat casting can make investment casting quite economical.
- The smooth surface finish can reduce the need for further machining or surface finishing.
The mold for sand casting is made of sand. Sand has some flexibility, so when the liquid metal cools and hardens, there are fewer cracks, tears, and other defects. Sand casting has the following advantages:
- Larger castings can be produced by sand casting.
- Sand casting is less expensive in short runs, especially.
- The cost of post-cast tooling is lower.
- Both ferrous and non-ferrous metals can be used.
What are the differences between investment casting and sand casting?
Design for production: In investment casting, ceramic shells are formed from the liquid slurry, so they can be shaped in almost any way, and engineers have great freedom to design complex structures and shapes. Sand casting parts are often designed to be tapered so they can be removed from a sand mold easily and with less friction. Casting parts with internal cavities or voids is more difficult. In sand castings, a suitable core is inserted into the mold to form the internal structure, sometimes multiple cores are used.
Weight: Unlike sand casting, investment casting can produce castings weighing less than 450 grams.
Surface finish: It is important to note that the surface of investment casting differs from that of sand casting. Because of the material of the mold, the surface of investment casting parts is smooth and can meet high tolerance requirements. Castings can be used immediately after being removed from the gate and blasted. Sand casting requires splitting the mold apart to release the castings, so the parting line is more apparent. Since the sand is rough, the surface is also relatively rough, requiring additional time and money to process.
Cost: Investment casting costs more than sand casting because of its complexity and preparation process.
A professional precision foundry with nearly 20 years of experience, Hulk Metal is certified ISO-9001 and is generally superior to other casting methods in terms of product details and surface finish. If you need investment casting parts, we can provide you with a one-stop solution from mold design to finished castings, machined castings, heat treatment, and surface treatment, as well as a one-stop solution for your investment casting parts. Feel free to contact us if you need assistance with your investment castings.
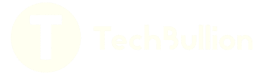