The creation of high-quality plastic components that can be used effectively and sustainably is the primary goal of plastic injection molding.
At every stage of the production process, it helps to improve output with great consistency and affordability. When compared to other molding techniques, plastic injection moulding company is a flexible approach with a number of advantages.
The procedure used in this moulding is very straightforward and trustworthy because it is a successful procedure that aids in the improved growth of suitable parts.
It combines the most recent trends and develops in accordance with business needs, which is why manufacturers really appreciate it while creating various plastic parts. The employment of new tools and equipment by numerous manufacturing firms has contributed to the general enhancement of the development process.
One of the efficient methods for creating plastic parts that meet corporate needs and criteria is plastic injection molding. High performance and efficiency are improved by the use of modern tools and equipment and the introduction of new features.
The functioning and uses of the manufacturing process are explicitly examined using some approaches. The following are the major advantages of plastic injection molding:
1. The Power to Create Complex Geometry
One of the key advantages of plastic injection molding is the capacity to create distinctive items with intricate details and challenging geometry. Due to the tremendous pressure that injection molds are subjected to, complicated designs can also be effectively designed with the right details.
2. Quick and High-Efficiency Production
The increased productivity and quick production of plastic injection molding, where the molding process is completed efficiently without wasting time, are two of its key advantages.
Once the injection molds are created with the demands of the customer in mind, the remaining molding procedure may be completed more quickly and effectively.
3. Being economical
Machines and other instruments, primarily in the plastic injection moulding process, can be used to lower the overall cost of manufacturing.
The manufacturing cost can be decreased at each level of development because the lone operator simply needs to oversee the entire procedure while employing a small number of workers.
4. Increased Versatility
To ensure that products are developed at the convenience of the customer, a customized product creation method is employed, where suitable colors and materials are used to meet particular needs.
The flexibility of the entire process will be improved by using cutting-edge features and the newest trends to create high-quality products while taking customers’ wants into account.
5. Minimal Waste
As the moulding process is discussed, it can be observed that a variety of tools are utilized to reduce the waste produced by the operation. To cut back on extra plastic and other garbage, eco-friendly actions are performed and operations are carried out as needed.
6. Low Labor Prices
Due to its ability to produce a variety of parts at a high level and a high output rate, which helps maintain cost-effectiveness, plastic injection molding has relatively low labor costs.
Because automated equipment and processes are employed for many tasks, little supervision is needed, which lowers labor expenses overall.
7. Increased Strength
When plastic injection molding is being developed, fillers can be employed in the injection molds to lower the density and increase the strength of the specific item. These extra tools are used to create pieces that need to be stronger and more durable.
8. Using several different plastics at once
Utilizing various plastic types at once is one of the main advantages of plastic injection molding. This contributes to the high performance and efficiency of a certain part’s enhanced development.
Key Take-Away
The use of injection moulding is essential because it requires minimal maintenance after production hence making it a more sustainable process.
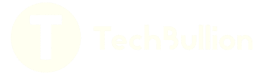