Six Sigma is a tool used to eliminate defects and errors in processes and improve business-critical metrics.
It has been known as the symbol of excellent management for many years, and its popularity has increased dramatically with time. Listed below are some facts that will give you a basic understanding of Six Sigma:
Origins
In 1980, Motorola engineers George Plata and Bill Smith, together with mathematicians Bob Galvin, John Leeke, and Ed Hines, developed the program in the United States.
At that time, Motorola was facing issues in developing semiconductor chips. They were producing 2.5 defective chips for every 1 million good ones. It prompted Motorola’s CEO to push the company into applying the statistical approach to solving problems. In 1983, Motorola manufactured chips with only three defective ones per 1 million good ones.
Milestones
In 1987, Motorola became the first organization to achieve the Six Sigma level in statistics. In 1995, General Electric Company obtained the certification as the primary framework for a quality program.
Six Sigma Principles
The practitioners of this method ideally follow certain fundamental principles:
- Focus: They should focus on the customers and design products accordingly. The main aim of methodology should be to satisfy customers and not just ship more products.
- Process: Change is required at both individual and organizational levels to change infrastructure, culture, and process.
- Measure: Quality should be measured in customer satisfaction, not just product performance.
- Define: It is essential to define the process before starting the change implementation. It would help you identify the project’s critical success factors and potential barriers before they take place.
- Act: The act phase contains all activities required for defining, measuring, and improving quality.
- Check: It involves checking the process to validate that it is working according to its designed specification.
- Keep records of all activities to measure progress over time.
Six Sigma Certification
The certification is given to an employee who has been trained and qualified by a master black belt, green belt, or yellow belt.
In 2003, Motorola was the first company to offer the Black Belt training globally by sending its engineers abroad to train organizations from Europe and Australia.
There are different levels of the certification, with ‘Black Belt’ being its highest. Individuals with the Black Belt designation have in-depth training in the tools and principles of the method. They are typically involved during all phases of a methodology implementation project.
Green Belts are usually involved in projects during the ‘Define’ phase, where they work closely with process owners to gather data and analyze customer requirements.
Yellow Belts work in the ‘Measure’ phase, where they help with data collection and analysis for metric development.
Black Belts are the highest level of certification and work across all phases to ensure successful implementation projects.
The Four Levels of Processes
The four levels of processes that can be improved through the methodology are:
- Level 1: The ‘Removed’ level is achieved when errors are removed from the process
- Level 2: The process is designed to meet customer requirements and constraints at the second level.
- Level 3: This represents an optimized state where the tools are applied to increase efficiency while maintaining quality.
- Level 4: The final level represents the state where the tools are applied to reduce defects and improve customer satisfaction.
“Eliminate” vs. “Reduce”
When using the tools, knowing the difference between ‘eliminating’ defects and ‘reducing’ them is essential. Elimination implies that the errors are no longer present in the process, whereas reduction denotes a lower defect level than what it was.
The ‘Pareto Principle
The Pareto principle, also known as the 80–20 rule, is a statistical concept that claims 80 percent of defects or issues in a process come from 20 percent of sources.
The Benefits of The Program
Some benefits of implementation include:
- Reduced costs: Identifying and removing defects early in the process can reduce costs by reducing rework, scrap, and warranty issues.
- Increased customer satisfaction: By identifying consumer needs better, the tool helps identify areas that companies need to improve upon to increase customer satisfaction.
- Improved decision-making: The ability to analyze data using advanced statistical tools makes it easier to make informed decisions.
- Improved communication: The intense focus on problem-solving helps employees communicate better and trust each other more. It also instills a questioning attitude where employees raise issues at the earliest, rather than going unnoticed until they become problems.
- Increased cross-functional awareness: The tool helps employees become more aware of other processes and functions within an organization. It provides a structured process to identify and solve problems, leading to better decision-making and problem-solving capabilities.
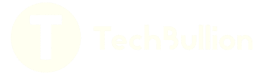