If you own a business, you should understand your inventory regardless of size.
You must be aware of the following:
- How much stock quantity do you need to order?
- How long will your products remain in the warehouse?
- How much money do you currently have locked up in inventory?
- How much money is actively losing value rather than boosting business profits?
A bit complicated, right?
However, you can easily get answers to all these questions by employing an inventory management system.
It aids businesses in determining which products to order, when to order, and in what quantities. It involves tracking inventory from producers and warehouses to the point of sale and is a crucial component of the supply chain.
Using the appropriate inventory management approach can result in supplying the right items in the proper quantity, at the suitable location, and at the correct time.
Some of the best inventory management techniques are:
1. FIFO and LIFO
Many businesses operate under the premise that the first products they create or buy should also be the first products they sell. This is known as the First In, First Out (FIFO) principle. Businesses that sell perishable items vulnerable to obsolescence often use the FIFO method.
On the contrary, the cost of goods sold is calculated using current pricing rather than the price you earlier paid for the inventory in the Last In, First Out (LIFO) inventory technique.
The product’s selling price will be higher if the price has increased after the first purchase. Tax liability reduction is the major reason for companies to use LIFO. So, when permitted, LIFO accounting is typically used for nonperishable goods.
2. Just-in-time (JIT) inventory management
In this order management process, working closely with suppliers is necessary to ensure that raw materials arrive at the time manufacturing is supposed to start, but not earlier. The purpose is to hold just enough inventory on hand to fulfil demand.
So, all manufacturing or service system components are connected to JIT. They share information and depend on one another to produce effective results.
Originating in Japan, the corporate concept seeks to improve operations continually and involves all employees, from assembly line workers to the CEO. The name Kaizen, which means “change for the better,” is the source of this technique.
3. ABC analysis
You can use an ABC analysis to identify which items are most and least useful, giving you a better insight into where to concentrate your time and energy.
Here is a general approach to sorting your products into different segments, which will change based on the business:
- Category A: High-value goods that do not require a lot of storage space
- Category B: Products of moderate value that require a typical amount of storage space
- Category C: Low-value items that require a lot of warehouse space
4. Consignment inventory
It is a supply chain strategy or business arrangement referring to the transfer of products from a consignor (such as a wholesaler, manufacturer, or supplier) to a consignee (such as a retailer) for sale.
The items still remain the consignor’s property, and the consignee will only be charged for them when sold.
Accounting for and managing consignment inventory may be challenging, especially if you sell both consigned and non-consigned items. So, if your company plans to combine the two, using an inventory management app could be beneficial.
5. Cross-docking inventory management
This technique practically removes the need to keep inventories.
When goods are transported to a warehouse, they are promptly processed and prepared for shipping. Moreover, they are often reloaded onto other trucks parked at the same warehouse.
Cross docking speeds up the distribution process, but important functions like quality control and inventory management should not be skipped. It still needs a great deal of cautious handling and preparation.
- Truckloads arrive at the docks near the warehouse’s entrance.
- Products are unloaded, sorted, and loaded onto trucks that are waiting on-site.
- Lastly, freshly loaded trucks are dispatched to the clients.
Cross-docking is not difficult, but it is not simple either. It demands perfect organization and military-style accuracy.
6. Perpetual inventory management
Every purchase and sale of goods is automatically and instantly recorded in a perpetual inventory system used to maintain and record stock levels.
The inventory management system tracks a change in inventory levels in real-time for each transaction.
For all sizes of e-commerce firms, a perpetual inventory system offers a number of benefits. For example, it assists in eradicating labour expenses and human mistakes.
Unlike periodic inventory management, perpetual inventory does not require manual adjustment except for the difference in physical and system stock levels.
7. Economic order quantity
This inventory management involves purchasing the optimal number of units to satisfy the demand. Simultaneously, it should also reduce inventory expenses, including holding costs, shortfall costs, and order costs.
Demand, ordering, and holding costs are all taken into account in the economic order quantity calculation, and they should remain constant.
EOQ is a critical cash flow instrument. The equation can assist a business in managing the amount of cash held in the inventory balance.
So, when EOQ reduces the amount of inventory, the money saved can be invested or utilized for other company needs.
Final words!
If you want to deliver your clients the desired experience, inventory management is essential whether you are a brick-and-mortar store, internet, or multichannel company. You will not succeed without using inventory management methods.
Additionally, to make the outcomes of these inventory management techniques viable and enhance them, investing in an inventory management app is essential.
The app will allow you to manage all your inventory on a single platform and improve business.
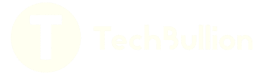