The injection mold material cost, processing cost, and taxes do not solely determine the cost of a mold. It is important to consider additional factors such as labor and design costs. These costs contribute to the overall expenses associated with mold production and should not be overlooked when calculating the total cost of a mold. So, here are some of the ways to reduce injection mold costs.
1. Rational Design of Products: Rational product design is one of the most impactful ways to minimize mold costs. It involves optimizing the product’s design to ensure efficient and cost-effective mold production. Companies can avoid costly modifications and simplifications later by considering the complexity of injection molded parts material selection, and manufacturing feasibility during the design phase.
The rational design also involves reducing unnecessary features, consolidating parts, and using standard components, which can significantly reduce mold complexity and manufacturing time.
2. Reduce Design Changes of Products: Design changes during mold production can be expensive and time-consuming. To minimize these changes, it is crucial to have a robust product development process in place. This involves thorough design reviews, prototyping, and testing to identify and address potential issues before starting mold production.
Effective communication and collaboration among the design, engineering, and manufacturing teams can help streamline the product development process and reduce the need for design changes, ultimately reducing mold costs.
3. Improve Mold Design: Investing in improving mold design can lead to significant cost savings. Utilizing advanced design software and techniques can help optimize mold design for better efficiency and performance.
Design enhancements, such as incorporating cooling channels for faster and more uniform cooling, reducing cycle times, and optimizing the ejection system, can improve productivity and reduce costs in the long run.
4. Minimize the Number of Mold Trials:
Mold trials are a necessary part of the production process, but excessive trials can increase costs due to extended production time and material waste. To minimize the number of mold trials, we should conduct thorough simulations and analyses before starting production.
Virtual mold-filling simulations can help identify potential defects or issues early on, allowing for adjustments in design or process parameters. Additionally, rapid prototyping techniques, such as 3D printing, can provide a cost-effective way to validate the design and functionality of the mold before full-scale production.
5. Select a Stable Material Supplier:
Choosing a reliable and stable material supplier is crucial for controlling injection mold costs. Inconsistent material quality can lead to variations in part dimensions, defects, and increased scrap rates, significantly impacting production costs.
Working closely with a reputable material supplier who can provide consistent quality materials can help reduce the risk of defects and ensure a smoother production process. Establishing long-term partnerships with material suppliers can also lead to cost-saving opportunities, such as volume discounts or customized material formulations.
6. Product Qualification: Thorough product qualification processes can help identify potential issues and ensure the injection mold production meets the required quality standards. Implementing robust quality control measures, such as dimensional inspections, material testing, and functional testing, can help detect defects or deviations early on.
By promptly identifying and addressing quality issues, companies can avoid costly rework or product recalls, ultimately reducing overall mold costs.
In this way, reducing injection mold costs requires a comprehensive approach encompassing various stages of product development and manufacturing processes. Companies can achieve significant cost savings while maintaining high-quality standards by focusing on the points mentioned above. To know more about injection mold costs, contact Prototool, and they will give the necessary details.
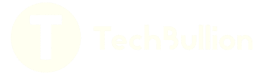