Traditional construction sites are notorious for generating significant amounts of waste — from off-cuts and damaged materials to surplus stock and excessive packaging. Managing this waste not only drives up costs, but also puts strain on the environment and delays project timelines.
Modular buildings take a more efficient and sustainable approach. By shifting most of the building process off-site into a controlled factory environment, it reduces waste at every stage — from initial planning through to final installation.
Here are five ways modular construction helps cut waste on-site.
1. Controlled Off-Site Construction Minimises Material Loss
A major source of waste in traditional builds comes from poor material handling. Deliveries arrive on cluttered sites where materials are exposed to the elements, damaged during transit or stored insecurely — increasing the risk of loss or theft. Over-ordering is common, and unused stock often ends up in the skip.
Modular construction avoids many of these pitfalls. Most of the work happens off-site in a well-organised factory setting. Materials are stored safely, kept dry, and handled by experienced teams following consistent build processes. The result? Less damage, fewer losses, and tighter control over materials.
Because modular factories produce in batches, they can reuse off-cuts and surplus across different builds. Materials don’t go to waste — they go back into production. It’s a smarter system that keeps waste to a minimum.
2. Precision Manufacturing Reduces Off-Cuts and Errors
On conventional sites, cutting materials on-the-spot leads to off-cuts and costly mistakes. If a measurement is off, large sections may need to be redone — wasting both time and materials.
In modular construction, every component is built to exact specifications using templates and automated cutting tools. This precision leaves little room for error and ensures materials are used efficiently. Wall panels, flooring, and roofing elements are all manufactured to the correct size, reducing off-cuts from the outset.
With the same team building similar units daily, processes become more refined. Mistakes decrease, leftover materials are better managed, and anything reusable is stored properly for future use. This contributes to both higher quality and lower waste.
3. Shorter Time on Site Means Less Temporary Waste
Traditional construction often requires extra materials for temporary protection and safety — plastic sheeting, fencing, signage, and coverings — much of which is single-use and quickly discarded.
Modular buildings drastically reduce time on site. Since the bulk of the work is completed off-site, the building arrives in sections that are ready for fast installation. Less time spent on site means fewer temporary materials are needed, and the risk of weather damage is lower.
This also reduces the number of skips required, eases pressure on site clean-up teams, and is especially beneficial in space-restricted or live environments like schools, hospitals, and commercial premises.
4. Modular Buildings Are Built to Be Moved and Reused
One of the most wasteful aspects of traditional construction is what happens when a building reaches the end of its life. Demolition produces huge amounts of debris, much of which ends up in landfill. Even refurbishment projects often involve stripping out reusable parts.
Modular buildings are designed differently. They can be moved, reconfigured, or repurposed with ease. If requirements change, the building can move with them. Units can be taken apart, added to, or rearranged without the need for demolition.
This reusability makes modular buildings a sustainable long-term choice. Companies across sectors are increasingly adopting them as part of their environmental strategies, reducing waste while maintaining flexibility.
5. Easier to Incorporate Sustainable Materials and Track Use
Traditional builds can struggle to meet sustainability goals. Rushed timelines, weather delays and unpredictable supply chains make it difficult to source and install sustainable materials consistently.
Modular construction changes that. In a factory setting, you have more control over every material used. From recycled insulation to FSC-certified timber and energy-efficient fittings, it’s easier to specify and implement sustainable options.
Standardised processes also make it simpler to monitor how materials are used, reused, or recycled — helping you meet sustainability targets and reduce the building’s carbon footprint over its full lifecycle.
Final Thoughts: Build Smarter, Waste Less
With rising material costs, stricter environmental regulations and growing demand for sustainable construction, reducing waste is no longer optional — it’s essential.
Modular buildings offer a forward-thinking solution. By reimagining how we build, they help you reduce waste, reuse resources and make smarter material choices from day one.
Modular Building Specialists Delivering Across the UK
At Phoenix Building Systems, we design and manufacture high-quality modular buildings that support both your project needs and your sustainability goals. Whether you’re looking to cut waste, meet environmental targets or build faster, we’re here to help you do it better.
Let’s Talk About Your Next Project
Get in touch with our team today to discover how modular construction can transform your approach to waste reduction and sustainability.
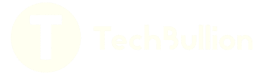