Imagine the warehouse that once operated manually now operates as an advanced technical solution that combines robotic systems and programming logic.
Sounds efficient. Right?
It shows that time-efficient operations serve as fundamental requirements in modern industrial facilities. Material handling speed and accuracy directly impact financial performance.
For example, it can affect retail network and e-commerce infrastructure management, as well as mass production capabilities. For this reason, advanced systems that handle materials are reshaping traditional operational procedures.
That said, these advanced enhancements provide operational transformations instead of traditional system updates. These advancements may include AI-powered robotics, automated systems, and software integration.
The result?
It leads to increased productivity while decreasing human error and accommodating rising customer demand.
Want to know more about these systems?
Here are some ways material handling systems transform industrial procedures and why adopting them produces the most beneficial choice for your facility.
1. From Fragmentation to End-to-End Integration
One of the most transformative shifts when it comes to material handling systems is the transition from fragmented, piece-by-piece upgrades to fully integrated end-to-end solutions.
Instead of engaging with numerous vendors for conveyors, robotics, and software, companies are using systems that can manage the complete system lifecycle. It operates with facility analysis, system design, installation, integration, and ongoing maintenance.
By taking this approach, your facility eliminates bottlenecks, and every component, like automated sortation equipment and software dashboards, works together efficiently. Similarly, a centralized control system allows for increased visibility, fewer downtimes, and easily scales operations during spikes in demand.
In addition, integrated systems help to lower implementation risk. For example, with only one point of accountability, businesses not only avoid costly delays but also operate with other essential requirements.
2. Innovation at the Core
The era of material handling systems goes far beyond the typical conveyors and forklift systems. Today’s cutting-edge technologies include:
- Automated Storage and Retrieval Systems (AS/RS): It reduces labor, minimizes the use of floor space, and maximizes inventory access.
- New Robotic Picking and Packing Systems: These are designed to significantly increase speed, precision, and order accuracy.
- High-speed Sortation Equipment: Such equipment is capable of processing thousands of parcels per hour with little error.
- Warehouse Execution Systems (WES) and Warehouse Management Systems (WMS): These systems harness real-time data and machine learning to smartly coordinate inventory movement and streamline complex logistics processes.
Thus, these advanced solutions increase operational efficiency and provide deep data insights. With it, you can also monitor performance, predict maintenance, and forecast demand.
Plus, businesses can fine-tune inventory strategies in real time to make smarter decisions, maximize throughput, and increase profit.
3. Customized Solutions for Unique Challenges
Every distribution center or manufacturing facility is unique. Each has a set of challenges unique to layout, product type, order volume, and available workforce. Modern material handling system providers recognize this and have increasingly focused efforts on tailoring solutions for each facility’s unique operation.
For instance, vertical lift modules are used for space-constrained warehouses, where you can utilize the overhead space. Moreover, facilities can utilize autonomous mobile robots (AMRs) for facilities where workflows are dynamic, and they can navigate through evolving layouts easily.
On that note, these systems are highly customized setups for current efficiency and support future scalability.
What’s more?
The customization is extended to modular system architecture, allowing businesses to scale up or reconfigure systems within minimal disruption of facilities. It enables businesses to adjust rapidly to changing market demands, offline peak demand, or long-term growth without expensive overhauls and downtime.
4. Supporting Scalability and Growth
A core advantage of modern material handling systems is scalability. It is a necessity because as businesses grow, their operational requirements change.
Suppose your business used to scale well for 100 daily orders, but the demand increases to 1,000 orders per day. In that case, your system should be able to support the new demand.
For this reason, today’s material handling systems are designed to seamlessly scale with no performance loss. Scalable systems are designed in a modular fashion to allow for easy integration of automation components, such as robotic arms, conveyor lines, and vertical storage units.
It is to handle increased order volumes. These also facilitate integration with new technologies and new data sources as the business becomes agile and future-ready.
Moreover, cloud-based platforms provide a centralized view and management of operations across multiple sites. This way, such systems improve coordination, standardize performance metrics, and support faster, data-driven decisions during complexity and supply chain volatility.
So, with the right system, companies can grow with confidence, knowing that their infrastructure will grow with them.
5. Enhanced Safety and Workforce Support
While speed is important in material handling innovation, so is safety. On that note, ergonomic automation helps reduce physical strain for workers, which reduces injury rates and increases morale.
Dangerous or repetitive tasks can also be performed by robots, as well as smart sensors and vision systems, which help prevent accidents. Further, automation acts as a solution for labor shortages and allows the existing staff to concentrate on more complex tasks.
That said, modern systems do not replace jobs. Rather, they enhance the workforce’s value and allow employees to collaborate with intelligent machines to work more efficiently.
Conclusion
Modern material handling systems are more than just logistics tools—they are strategic enablers of growth, efficiency, and resilience.
They help by providing end-to-end solutions and innovation, supporting scalability, and enhancing the safety of the workforce. In other words, they’re setting the pace for the future of logistics.
So, are you looking to bring next-level efficiency to your operation?
Now’s the time to use these modern material handling systems that can be tailored to your business needs.
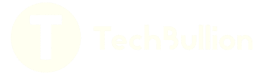