Moving your business, whether you’re heading across town or across the country, will take a lot of planning and organizing. Ultimately, the cheapest way to do this may be to have two facilities open for a time so you can move slowly with as little disruption as possible.
Digitize When Possible
Take a hard look at your archival data. Do you really need paper copies of receipts, purchase orders, and packing lists? Do you really need to keep paper copies of payroll records? A secured electronic filing system, stored in the cloud, can reduce the load of paperwork to a computer, an internet connection, and a printer.
Start early on this and invest in a high-speed scanner. Take the time to set up file name and date protocols so you can easily search for information once you have scanned and shredded all this information. Consider getting a system that allows for Optical Character Recognition, or OCR scanning so you can dig in more deeply to find a lost document.
Make sure that your staff members doing the scanning have the time to
- scan the document and backup paper
- name the document consistently
- count the pages to avoid data loss
This process will not be quick. If you’re working in the new paperless system while you’re loading it with archival data, consider bringing in scanning staff on the weekend to lighten the load on the system.
Let Suppliers Redirect Your Inventory
Depending on whether or not you’re moving raw goods and tools or finished products, your simplest moving plan may be to allow your suppliers and delivery companies to relocate your stock to the new facility.
Of course, your security setup will need to include coverage for both facilities. If you’re going to be storing anything outside at your new facility, do make sure that the security is upgraded whenever possible. This may include
- security fencing and gates
- security lighting
- drive-bys by local police and security professionals
While this may be an investment because you’re making a double lease payment, you can also keep your business producing at least partial runs or shipments to keep your customers happy. You may have to do a short shutdown to move critical tools to your new facility, but you won’t have a long-term shutdown that will encourage your customers to look for a replacement.
As soon as you can schedule that shutdown, share that information with your clients to avoid jolting their supply line.
Pack What You Can On Your Own
Be ready to pack smaller things on your own. If you have an employee with strong moving skills, provide them with the time to go collect (free) moving supplies. Reach out to your attorney and accountant and put in a request for paper boxes. Boxes that contain 8.5 x 11 reams of paper are uniform in size and easy to stack.
Break down the move into small chunks. If you have some tools or raw materials that you need to hang onto for a specific seasonal project, relocate the whole project so you can start to load in for every department involved. Just one production run will take tools, raw goods, finishing, inspection, and shipping. Start small and use this project as your pivot point for your move.
Consider hiring a few temporary folks to load boxes. You want a full-time employee to direct where things go in the new space, but a moving crew with the tools and strength to safely load the truck will save a lot of stress and grumbling.
Move Slowly
Consider renting a truck for the long term and moving slowly. If your move is from your facility to a shipping container or directly to your new facility, packing slowly and moving things in small batches may be an ideal option.
If possible, consider making your move over a summer or holiday school break. You may have employees who have a student who has a break over the holiday; put them to work loading boxes in the truck. The student can earn a bit, the labor force can expand easily for the short term and your move can be convivial.
Do be aware that some employees will be unhappy about this, especially if their job is going to go away. If you know that an employee is resistant and possibly even slowing things down, move them to another project to speed up the move. The decision to move your business is never an easy one, but once you’ve made it, don’t let anyone get in the way.
Use Professional Services Wisely
In some cases, moving on your own can be destructively dangerous. For example, you may have a highly technical tool that needs to be taken apart to ship. If you’re bringing out technicians to disassemble and reassemble it anyway, see if they will give you a quote to move the tool. Even if something goes wrong, they will carry the burden and liability.
Get quotes on moving your company vehicles, especially if you have to move over water. Whether you’re ferrying cars over water in the northwest or looking for Hawaii car transport options, vehicle movers can increase the efficiency of moving your fleet.
If you’re planning to move your fleet of service vehicles loaded with gear for your business, do take the time to get everything serviced. Oil changes and fluid checks are critical; make sure you also get the suspension and steering checked out before you load these vehicles down with containers and tools.
The supplies necessary for moving your business can actually be quite cheap. If your business cannot grow anymore in the current location and relocation is critical to expansion, finding the space for these free shipping tools may be the biggest challenge to getting started. Communicate your intentions clearly and loop in as many employees as possible.
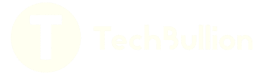