One of the essential factors in maintaining successful operations is correctly estimating and maintaining your equipment’s reliability. What is equipment reliability, you may ask? Well, it is the period; the equipment should perform its function without developing a fault.
In other words, it is time the machine was rated to be used. However, this time can be significantly improved through various tips and tricks. The importance of improving this time is great, as it can help to increase the efficiency of the operation and lower costs, thereby increasing marginal profit.
This article will discuss some of the most common tips and tricks to safeguard businesses from financial loss by:
- Implementing your operational routine
- Ensuring that your equipment lasts longer than what it is rated for and gives you its maximum output.
Maintenance Planning & Schedule
Proper recording and planning are the keys to a prolonged life span of the equipment. Maintaining the service logs for all the maintenance allows you to judge the output of your equipment effectively.
Moreover, make it a habit not to miss any due services as well, because if you miss your services, you will also be missing efficiency. Another benefit of timely maintenance planning and scheduling is that it saves you money on repairs, which would have resulted from the excessive wear and tear your equipment would have suffered had you not given it proper service on time.
The benefits of planning ahead of schedule include the following:
- Regular Inspection minimizes the changes in the breakdown.
- Maintenance Planning helps in quality control.
- Proper Maintenance records can help increase the efficiency of the piece of equipment.
Ways to Improve Equipment Reliability
1. Use Data for Decision Making
Data is essential when it comes to making decisions regarding your equipment. Diagnosing a problem is easy; however, a skillful maintenance team should be able to record the number of times the equipment has failed, the frequency of the damage, and other metrics.
After this, the team should analyze this data to understand better the correlation between an equipment’s service history, breakdowns, and efficiency. Numbers can tell us a lot about a piece of equipment and whether it will be feasible to work with in the long run.
Moreover, this data can be used to make decisions regarding the equipment. Some of the essential data metrics, which a technical team might take into account when presenting a root cause analysis, may include,
- Frequency of Failure
- Cost of Failure
- The time cost of the solution
2. Educate Employees and Work on their Skill Set
This point is the most important preventive measure you can take when it comes to avoiding an equipment malfunction and increasing its reliability. These equipment machines, after all, are made of metals or other materials and hence need due attention and care daily.
Your employees should be trained to handle machines with care and due diligence. Rough handling of equipment could significantly affect its degradation and wear and tear.
Your employees should be able to:
- Spot the telltale signs of any problem before it occurs
- To manage it, and
- Do damage control before the situation deteriorates.
This will help you save on repair costs and increase the equipment’s reliability.
You can train your employees in-house or train them elsewhere with qualified technicians for better handling of your equipment. This investment will surely pay off.
When your employees become more skilled in handling the equipment and preventing it from working at its total efficiency, they’ll save you money in the long run.
Source: Flickr
Workshops, training, and sessions are a great way to educate your staff on equipment handling and risk management. Apart from this, you can announce incentives, such as bonuses for those participating in such workshops.
This way, you can create healthy competition and ensure that your equipment is in good hands.
3. Precision is Important
Invest in tools that are essential for the maintenance of the equipment. Indeed, you must have heard that a wrench and hammer are all you need in these situations. However, that’s not true. This equipment can range from simple machinery to highly complex systems, which require sophisticated tools to be worked on. You should invest in the proper repair kits and use standard parts for this equipment to prolong its life and not affect its reliability.
These fancy tools might seem like a bad investment, but you will understand their importance when they save you a big trip to the repair shop.
There are innovative tools that utilize lasers and other tools for precision. Precision is the key to a successful repair operation and dramatically affects your equipment’s longevity.
4. Lubricants and Motors
One of the parts where you can expect the most trouble is the motors; hence, it is vital to get them checked on their due date and get them cleaned on time. Stuck debris can cause a lot of damage to the motors and reduce their efficiency by a considerable margin.
There are specialized cleaning tools for electrical and other motors these days. They will help you keep your motors and, by extension, your equipment in excellent condition. Apart from this, lubricants are another vital aspect not to neglect when it comes to your equipment’s longevity and efficiency.
Most people think it is okay to get cheaper oil for their machines. But, in the futile process of saving money on oil, they unknowingly destroy the internals of their equipment with subpar lubricants.
Therefore, it would be best if you made it a habit to invest in only the best lubricants for your machines.
Conclusion
Now you know about the importance of equipment reliability and tips for improving it. Some of the essential tips to increase the reliability of the equipment include:
- Regular inspections by certified maintenance consultants
- Training your workforce regarding the proper protocols and risk management to prevent accidents and loss.
Besides these tips, think about hiring a maintenance consultant.
These experts can help you with maintenance planning and scheduling, making sure your operations run smoothly and effectively. They will look after your equipment and come up with assessments based on rigorous testing models, that enhance your equipment’s efficiency under various conditions.
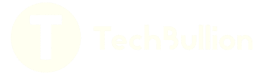