Safety is one of the significant concerns for industrial plants where risks of accidents abound. The risk levels vary according to the raw materials, processes, and end products. Chemical plants face a higher level of threat because of evident reasons. Many times, raw materials and end products are hazardous to human health, and industrial processes are prone to mishaps.
According to data compiled by the Environmental Protection Agency, the US averages one chemical accident every two days. Unfortunately, industrial leaks and spills are a part of these statistics, but manufacturers sometimes get complacent about such events.
In December 2020, the Wacker Polysilicon North America plant located in Charleston, Tennessee, was found responsible for the deadly release of a toxic gas. Two workers were seriously injured, and one died when trying to climb down a 70-foot-tall tower during the leakage.
The incident highlighted the significance of safety for chemical plants. As a factory owner, you need to take ownership of the well-being of your workers, visitors, and the community.
Here are a few proven strategies chemical plant owners can rely on:
Identify Potential Hazards
International Labor Organization statistics indicate that nearly 1 billion workers are exposed to hazardous substances, such as chemicals, pollutants, dust, vapors, and fumes. Not paying attention to these hazards is the worst mistake chemical manufacturers may make. Conversely, identifying them takes you a step ahead of your safety goals.
Identifying hazards requires a thorough assessment of products and processes. It includes the following steps:
- Reviewing materials and chemicals used in the production process for toxicity, flammability, reactivity, and other properties
- Checking the machinery and equipment to assess the risk of overheating, mechanical failure, and other last-minute issues
- Conducting an in-depth analysis of the production process to evaluate the possibility of spills, leaks, or explosions
- Considering human error factors such as improper handling of equipment or chemicals during the industrial process
Mitigating Hazard-Specific Risks
Once you have a checklist of potential hazards in your chemical plant, you can create a plan to mitigate hazard-specific risks. Although devising the plan requires a comprehensive approach, the effort is worthwhile. After all, you can save millions and protect your reputation by preventing accidents in your plant.
For example, implementing engineering controls such as ensuring good ventilation and having proper chemical storage systems can minimize production-related risks. Worker training can address the problem of human error. Installing equipment like ultrasonic flow meters ensures accuracy in the measurements of chemicals during the industrial process.
SmartMeasurement notes that plant owners should consider factors such as the amount of suspended solids or gas bubbles when choosing an ultrasonic flow meter. Selecting an apt one makes all the difference to plant safety.
Maintaining Equipment and Machinery
Setting up equipment and machinery in a chemical plant is only a beginning. Maintenance of your equipment and machinery is another measure to enhance safety in your chemical plants. Well-maintained machines can keep the system running smoothly without the risks of leaks, spills, and measurement flaws.
Studies show that predictive maintenance is significantly cost-effective, with a potential saving of 8-12%. It also results in a tenfold increase in return on investment. Besides boosting efficiency and minimizing accident threats, timely maintenance saves your plant from compliance issues.
Promote a Culture of Safety
Over the years, most businesses have learned the value of building a robust culture. A positive culture is the top priority for business seekers. Since chemical manufacturing is inherently risky, promoting a culture of safety is imperative for manufacturers.
A safety culture includes several things, such as employee involvement, training and resources, and recognition of safe behavior. At the same time, it is also about leadership commitment, regular safety audits, good communication, and continuous process improvement.
By prioritizing safety at all levels, chemical plants can protect their employees, reputation, and the environment. It ensures compliance with safety regulations, preventing penalties and legal hassles for your business. A culture of safety also enhances your employer brand, which helps attract and retain the best employees for your business in the long run.
Summing Up
Accidents are a real threat to chemical factories because of hazardous products and complex processes being a part of work. However, safety can become a hallmark of your plant with the right approach and a lot of caution.
All you have to do is implement these practical and proven strategies to create a safe workplace for your employees. Profits, growth, and reputation will follow effortlessly once you start going the extra mile with safety.
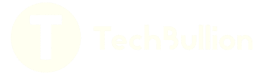