Inventor Denis Lvov, PhD has developed a microwave 3D printing technology that can operate virtually anywhere—from jungles to outer space.
According to Protolabs’ 2024 report, the global 3D printing market reached $24.8 billion, with an average annual growth rate of 21%. These figures confirm that the 3D printing market continues to show steady growth and significant potential for further development. And among the participants in this “race,” clear leaders are already emerging.
Denis Lvov, PhD — holder of multiple patents in Russia, the US, and the EU — is the creator of a fundamentally new technology called Selective Microwave Melting (SMM). His groundbreaking method of metal 3D printing using microwave breakdown has already been licensed by industrial companies in Russia, the Czech Republic, and Armenia. Lvov himself has taken part in prestigious forums, including FormNext in Frankfurt, Germany, and the 3D Fab+Print Moscow conference.
We spoke with Denis about how he discovered a new method for creating metal components, why microwaves are better than lasers, and how his technologies might one day aid lunar exploration.
Your scientific article “Conceptual Approaches to the Development of Models of Gas Flow Dynamics in Inflated Devices,” published in IRJMETS, explains the use of a microwave field for localized, controlled heating of metal powder. How did the idea of using microwave radiation for metal 3D printing come about?
I was first introduced to 3D printing back in 2008. The first 3D printer I bought used the fused deposition modeling (FDM) method to print plastic layer by layer. I still remember the magical feeling when something tangible began to grow layer by layer from nothing—from the digital void into the real world.
This subject fascinated me, so I began to study computer-aided design (CAD) on my own and started diving into the nuances of 3D synthesis using different materials and methods. What intrigued me the most was metal 3D printing, as it opened up virtually limitless possibilities. My thoughts on how to make metal 3D printing more accessible led me to search for a fast and inexpensive way to heat metal powder precisely where needed.
In discussing your discovery, you mentioned a study you conducted during your postgraduate research, where you explored the possibility of using microwave discharge to generate high-temperature plasma. How did you apply that knowledge in practice?
From my previous scientific work, I knew that microwaves were well-suited as a heat source. Simply put, my research focused on how microwaves could be used to inject energy into plasma—within known limits—to heat it to virtually any temperature, even high enough to initiate thermonuclear fusion. At the time, the research remained at the lab-experiment stage. Later, I decided to apply this knowledge to 3D printing.
Previous studies in this area had shown that magnetron radiation is difficult to focus. That led me to realize that instead of using microwaves themselves as the heat source, I should use microwave breakdown—a specific type of discharge in a microwave field. It is compact and controllable. I immediately tested the idea using improvised materials: a setup made from a tin can, a nail, and a pinch of fine metal shavings was placed inside a kitchen microwave.
When the microwave was turned on, a microwave discharge ignited—just as expected—in the gap between the nail tip and the can. It instantly fused and sintered the shavings into a small metal bead. That simple contraption became the “first prototype” of the microwave 3D printer, and the bead was the first object ever made using the selective microwave melting (SMM) technology.
You showcased your first printer at the world’s leading 3D printing trade fair — FormNext 2019 in Frankfurt am Main — where the device was highly praised by industry experts. Were there any challenges in building the first machine? What took the most time?
Since I built my 3D printer essentially on the mechanical base of an existing, mass-produced powder-based 3D printer, I managed to complete it in a record time of just two and a half months.
The scientific research and experiments, however, took a bit over a year. It was also crucial to file patents for everything that had been developed. After extensive study, discussions with experts, and with the help of a functioning prototype, I was able to prove the viability of the concept.
Today, the technology of selective microwave melting as a method for producing parts from powder has been patented by me in Russia, the EU, Canada, and the United States.
Around that time, you caught the attention of SLM Solutions — a company long considered a monopoly in the field of laser metal 3D printing. What interested them in your technology?
They had been searching for an alternative to lasers for quite a while. The problem with laser radiation is that it’s difficult to scale, especially when you want to build a high-power printer for producing large parts. They had experimented with microwaves themselves but were unable to control the location of the discharge — in their trials, they only got random sparks all over the build chamber.
For their engineers, it came as a surprise that in our setup, the discharge would ignite and extinguish precisely where it was supposed to. Their interest was understandable: beyond manufacturing the machines, they also held the main patents for SLM technology, which were expiring — while mine were just beginning.
But bureaucracy got in the way: large companies from the EU and US typically acquire promising technologies by buying out the companies that developed them. However, there is no standard procedure for acquiring companies — let alone independent inventors — from Russia.
Your team claims that the cost of the printer can be reduced tenfold, and its productivity increased by a factor of 100. That sounds almost unbelievable. How is that possible?
Printers based on microwave breakdown do not require complex optics or high-powered lasers. All you need is a power source of the appropriate capacity.
An additional boost in process efficiency comes from the fact that the size of the “breakdown” zone at the fusion point can be controlled electronically, almost instantly. This means you can weld the outer contour of a part precisely with a 100-micron spot, and then rapidly fill the interior with a spot up to 4 mm in diameter. In other words, the system’s productivity compared to laser-based setups increases by hundreds of times.
Among your patents are developments not only related to 3D printing, but also to the control of liquid and gas flows. Are you laying the groundwork for future manufacturing with this?
Everything is interconnected — phenomena in electromagnetism and gas dynamics are even described by equations of the same type. To work effectively with microwaves and plasma, you need to understand how gases behave and how energy propagates through a medium. This is directly related to my work in flow modeling.
For example, we simulate how a discharge is formed, what electrical currents arise, and how heat spreads through the powder. Without this understanding, the development of the SMM technology would have been impossible.
What is the most ambitious project you believe could be implemented using this technology?
I would highlight the potential of using my technology in the future colonization of the Moon. For building lunar bases, you need construction material — and delivering it from Earth is extremely expensive.
We need the ability to build from what is already available on the Moon — that is regolith. There is plenty of it, and it does not need to be milled — it is already in powder form. You can construct buildings from it.
The 3D printer requires nothing but electricity, which is easy to generate using solar panels. Since there is no atmosphere on the Moon, the efficiency of solar panels will be even higher — or a nuclear reactor could be used instead.
What advice would you give to startups and investors looking for the next “big breakthrough” in 3D printing?
With metal and plastic printers, everything is already fairly clear: they will continue to become more integrated into our daily lives. It is amazing that with a minimal set of machines, you can even produce a rocket engine; an engineer can quickly prototype and test their design, and a broken part can be replaced right on the spot.
Their development will keep progressing toward higher productivity and lower costs, making the technology more widely accessible. One company already offers fully 3D-printed shoes — once that becomes mainstream, why would we need traditional shoe factories? All that is needed is a design, and people could print their shoes at home — even today.
I believe the next major breakthrough will come in the field of biological 3D printing, which could allow us to easily synthesize not only tissues and organs for medicine, but also food. One day, a typical kitchen might include a device that can 3D print your breakfast hamburger. And a pharmaceutical 3D printer might save you a trip to the pharmacy by printing your prescription pills at home.
I would also point out that the future of 3D printing lies in simplification. Working with early FDM printers was more of an art — requiring delicate manual calibration for each task and material, and careful tuning of numerous parameters in the control software.
Today, printers are already quite automated. The next step will likely be smarter printing software. What we really want is a program that not only generates supports but also automatically compensates for process-related distortions — such as thermal shrinkage, warping, and similar effects.
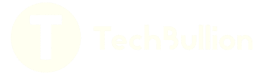